Figure Level Capacity Plan Figure shows the level capacity plan of a company manufacturing a product on produce to stock and sell basis In the first quarter aggregate demand is less than production and inventory builds up till the end of the First Quarters in the second third and fourth quarters are inventory levels Decline because production is less than the aggregate demandTwo aggregate plans are now being evaluated by Tiyendepamodzi advertising Level Capacity with backlog and Matching demand It costs Tiyendepamodzi advertising K0 for every Kwacha of sales on any category of advertising backlogged (delayedEach printer requires an average of 30 labour hours, and the manufacturing plant uses a backlog of orders to allow a level capacity aggregate plan This plan
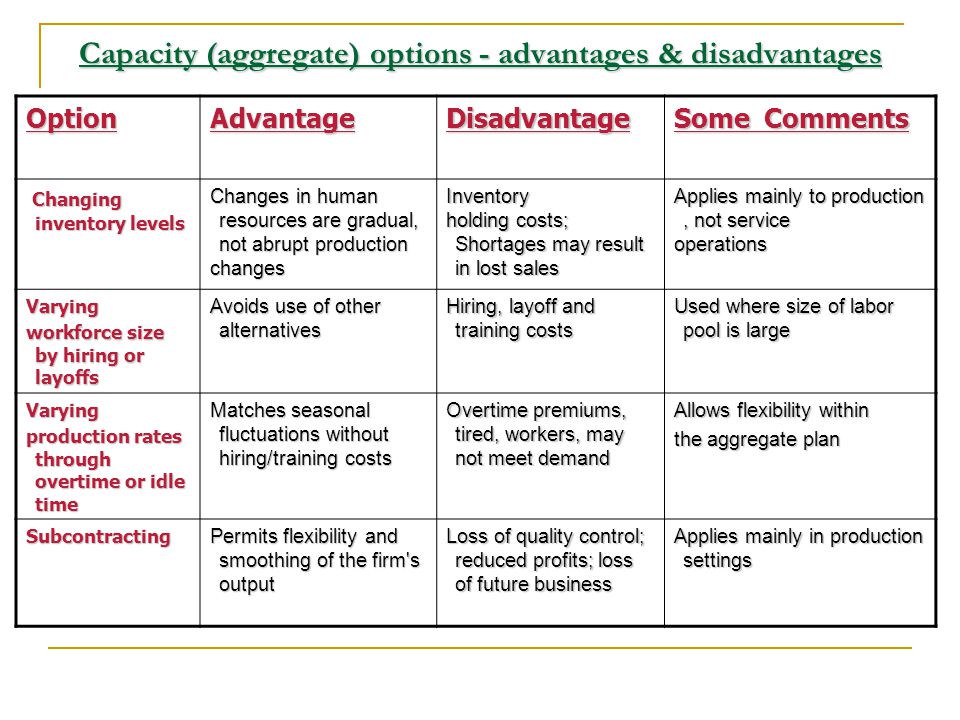
Aggregate Production Planning Ppt Video Online Download
What does aggregate rated capacity mean
What does aggregate rated capacity mean-10 Next level down in the planning process after development of the aggregate plan is _____ a) materials requirements plan b) engineering plan c) roughcut capacity plan d) master production schedule e) purchasing plan 11 For the level aggregate plan, fluctuations in demand are absorbed by _____ a) inventory and subcontractingIn this lesson, we investigate the process of developing a level production plan in this aggregate planning segment
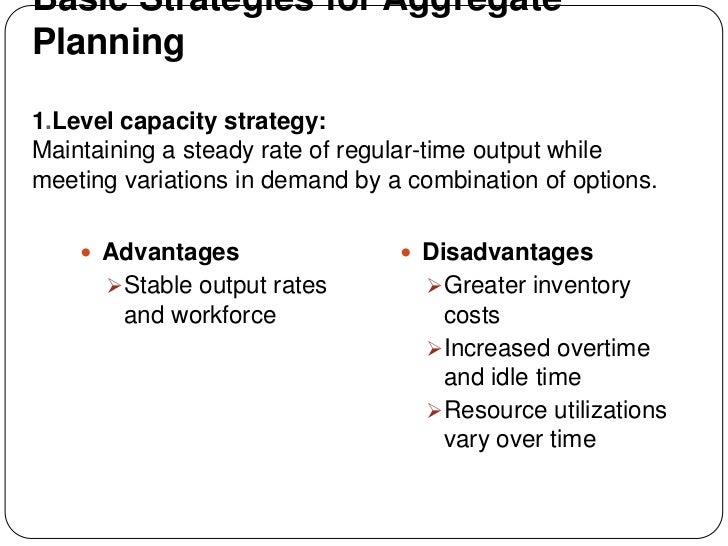



Aggregate Planning Report
Aggregate Planning Quarter 1 Jan Feb Mar 150,000 1,000 110,000 Quarter 2 Apr May Jun 100,000 130,000 150,000 Quarter 3 Jul Aug Sep 180,000 150,000 140,000 Master production schedule and MRP systems Detailed work schedules Process planning and capacity decisions Aggregate plan for production Aggregate Planning Figure 132 Product decisionsJan 04, 19 · • The role of Aggregate Capacity Planning is to Keep capacity utilization at desired levels and to test the feasibility of planned output against existing capacity • It is the process of planning the quantity and timing of output over the intermediate time horizon (3In other words, a level strategy is an aggregate plan in which production is uniform from period to period Firms like Toyota and Nissan keep production at uniform levels and may (1) let the finished goods inventory go up or down to buffer the difference between demand and production, or (2) find alternative work for employees
Apr 21, 11 · Defining Aggregate Planning Aggregate planning is the process used for managing schedule activities relating to demand and capacity such as analyzing, deploying, maintaining the timeline of the projects and operationsA hybrid aggregate plan uses options from both the level and chase aggregate plans It is used because we may not prefer to use a level or aggregate plan We can combine our preferred decisions from each plan Explain the procedure for developing an aggregate plan First, we choose the type of aggregate plan to useNMIMS SEP 21 SOLVED ASSIGNMENTS – Defining the concept of aggregate plan for operational capacity management, which strategy (Level or Chase) do you think would NMIMS SEP 21 SOLVED ASSIGNMENTS – Defining the concept of aggregate plan for operational capacity management, which strategy (Level or Chase) do you think would www
4 List the capacity options in aggregate planning 1 Hire and lay off workers 2 Overtime/slack time 3 parttime workers 4 Inventories 5 Subcontracting 5 List the main strategies for meeting uneven demand 1 Maintain a level of workforce 2AGGREGATE PLANNING Deciding on the level of capacity (eg, physical capacity or labor) of a firm and on how to readjust that capacity to respond to changing demand conditions A way of translating demand forecasts into a blueprint for staffing/capacity and production levels for the firm over a predetermined planning period AggregationList the demand options in aggregate planning?




Outline Role Of Aggregate Planning Role Of Aggregate Planning Logistics And Supply Chain Management Aggregate Planning Pdf Free Download
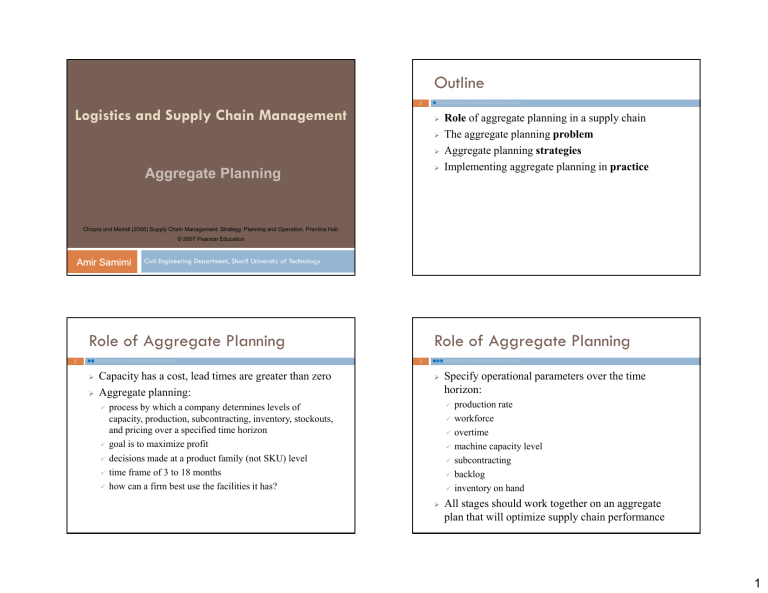



08
Aggregate Plan Strategies 1 Maintain a level workforce (Level Capacity Strategy) 2 Maintain a steady output rate (Level Capacity Strategy) 3 Chase Demand Strategy (Match demand period by period) 4 Use a combination of decision variables ChaseAggregate planning is a marketing activity that does an aggregate plan for the production process, in advance of 6 to 18 months, to give an idea to management as to what quantity of materials and other resources are to be procured and when, so that the total cost of operations of the organization is kept to the minimum over that periodA level strategy seeks to produce an aggregate plan that maintains a steady production rate and/or a steady employment level In order to satisfy changes in customer demand, the firm must raise or lower inventory levels in anticipation of increased or decreased levels of forecast demand



Sihombing15 Files Wordpress Com 08 08 Ch 7 Aggregate Capacity Planning Pdf
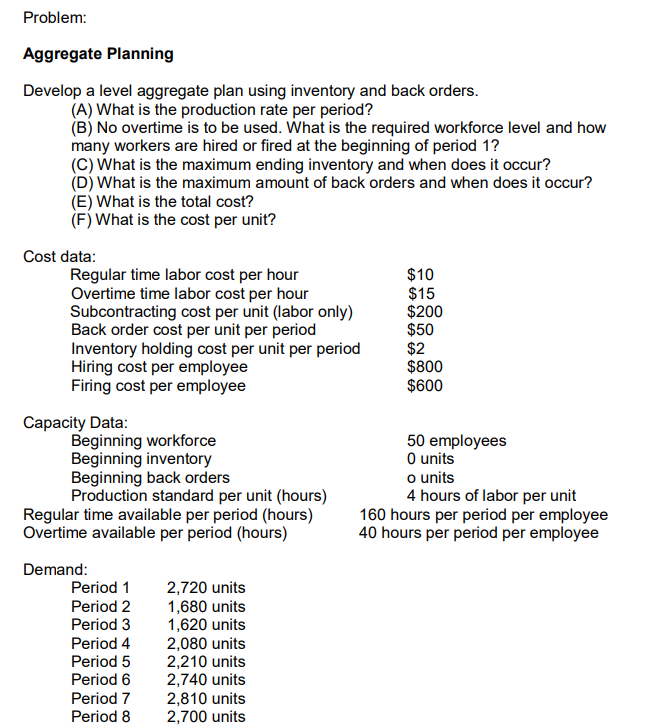



Problem Aggregate Planning Develop A Level Aggregate Chegg Com
A major component of aggregate planning is to plan aggregate production and inventory levels to achieve a desired level of customer service In preparing the aggregate plan, a major consideration is to check the desired production plan against the estimated capacityJul 03, 19 · Aggregate capacity management (ACM) is the process of planning and managing the overall capacity of an organization's resources Aggregate capacity management aims to balance capacity and demand inDisaggregating the Aggregate Plan Aggregate Planning Aggregate planning Intermediaterange capacity planning that typically covers a time horizon of 2 to 18 months Useful for organizations that experience seasonal, or other variations in demand Goal Achieve a production plan that will effectively utilize the organizations' resources to satisfy demand Sales and Operations Planning
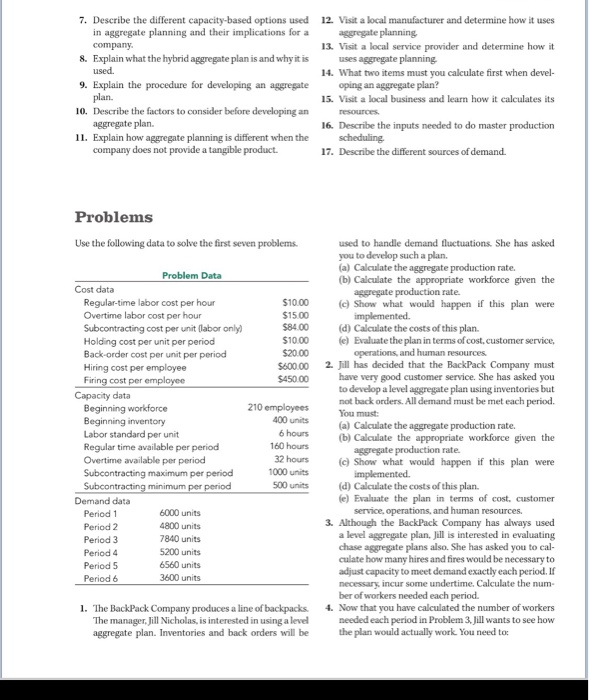



7 Describe The Different Capacity Based Options Used Chegg Com




Aggregate Capacity Planning Pdf Free Download
Mar 10, · The aggregate planning process helps to calculate capacity, for instance, how many units can be produced daily or in a week or a month Production orders cannot be constant throughout the year It will vary and this makes it difficult for the business entities to keep up with a similar production plan for all timesMay 31, 17 · Aggregate production plans facilitate matching of supply and demand while reducing costs Process of Aggregate production planning applies the upperlevel predictions to lowerlevel, productionfloor scheduling and is most successful when applied to periods 2 to 18 months in the future Plans generally either "chase" demand, adjusting workforceMar 04, 21 · A small manufacturing plant is considering their aggregate plan for the next fiscal year They are limited to a maximum number of 40 FTEs each quarter Their forecasted demand for next year is Quarter 1 2 3 4




Aggregate Planning An Overview Sciencedirect Topics



Myclass Dau Edu cswebdav Xid 4 2
Strategic Capacity Planning Aggregate Planning Long Range Medium Range Short Range How much & when plan Aggregate operations planMedium Supply network planning Forecasting and Four General Strategic Plans 1 Level – constant workforce/production level – fluctuating inventory levels 2 ChaseCAPACITY PLANNING Capacity is defined as the ability to achieve, store or produce For an organization, capacity would be the ability of a given system to produce output within the specific time period REDUCING RISK WITH INCREMENTAL CHANGES AGGREGATE PLANNING STRATEGIES AGGREGATE PLANNING Aggregate planning is an operational activityAggregate Plan Aggregate planning refers to the process of developing, maintaining, and analyzing the approximate scope of the operations of a company It usually contains targeted sales forecasts, inventory levels, and production levels Aggregate planning determines capacity and then minimizes the cost by balancing them against such capacity
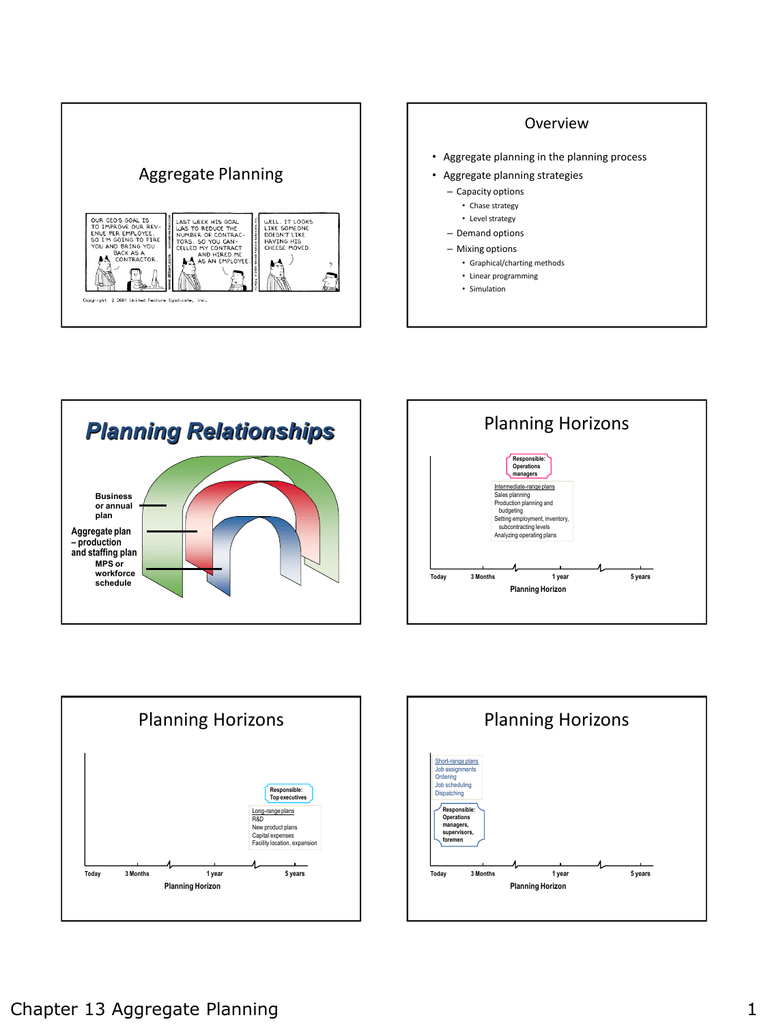



Planning Relationships Planning Horizons Aggregate Planning
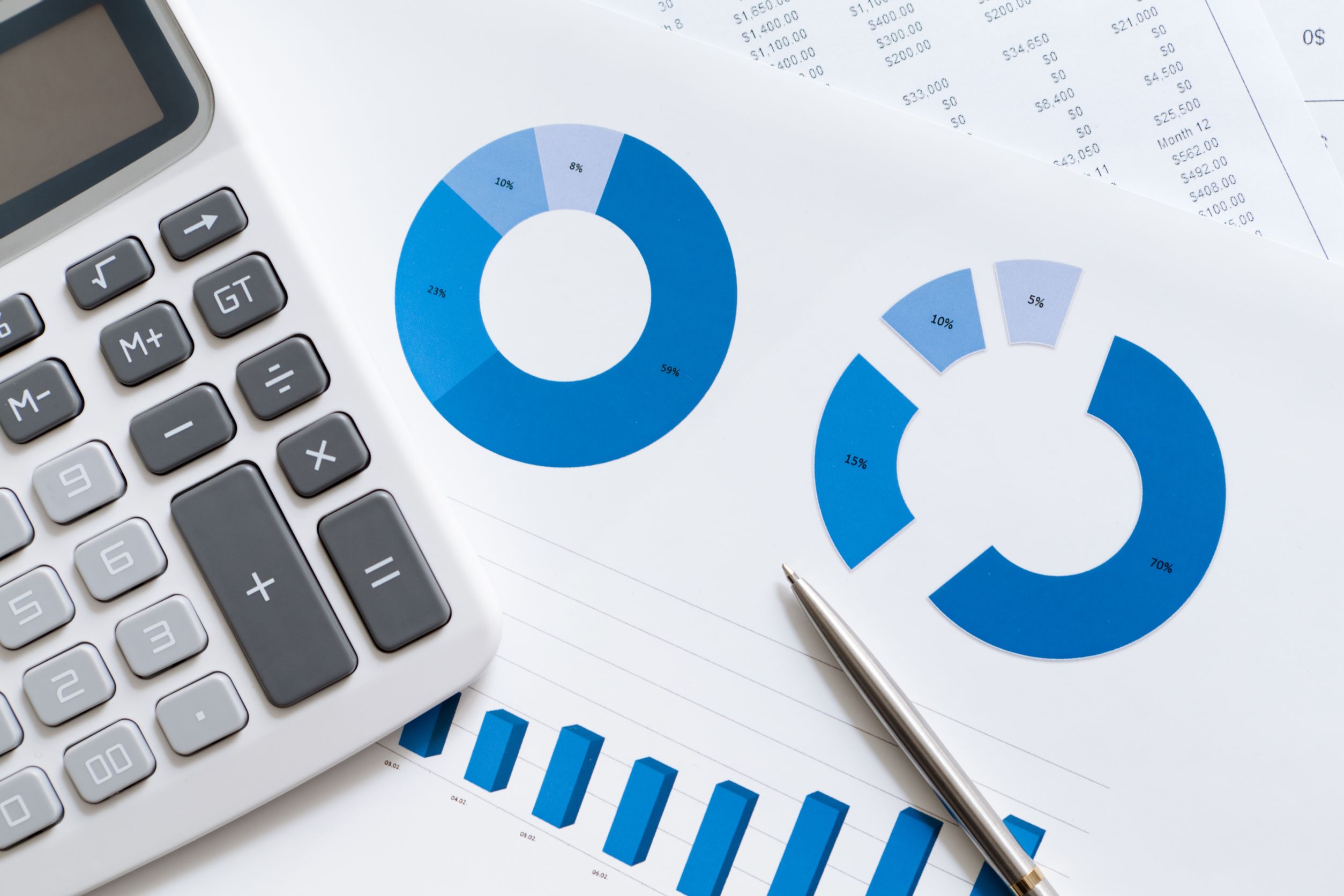



Advantages Of Aggregate Planning
Feb 04, 15 · Aggregate capacity is the total amount of capacity required or available to carry out a function It also tells about the 3 best strategies for aggregate planningThey are level strategy, Chase strategy and hybrid strategyThe plan must be in units of measurement that can be understood by the firm's nonoperations personnelAggregate units of output per monthDollar value of total monthly outputTotal output by factoryMeasures that relate to capacity such as labor hoursOct 17, · 21 A company is interested in developing a quarterly aggregate production plan but they arent sure if level capacity or matching demand would be better They have the following information available regarding their production operation Number of working days per quarter = 65 days Number of
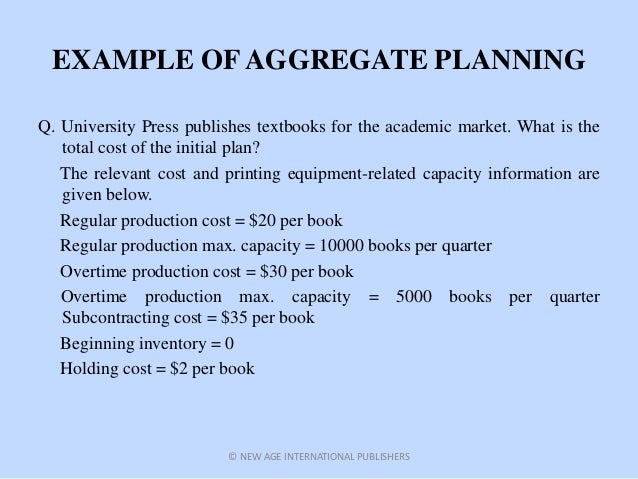



Capacity Aggregate Planning




Aggregate Planning An Overview Sciencedirect Topics
Jun 21, 21 · Question A local company makes athletic clothing and they are preparing aggregate production plans on a quarterly basis for the coming year for their line of women's wear They have the following information available to develop a level capacity and a matching demand plan Number of working days per quarter = 65 days Number of hours per day1 Price 2 Promotion 3 Back orders 4 New demand;Aggregate Planning level capacity and chase demand strategy A small manufacturing plant is considering their aggregate plan for the next fiscal year They are limited to a maximum number of 40 FTEs each quarter
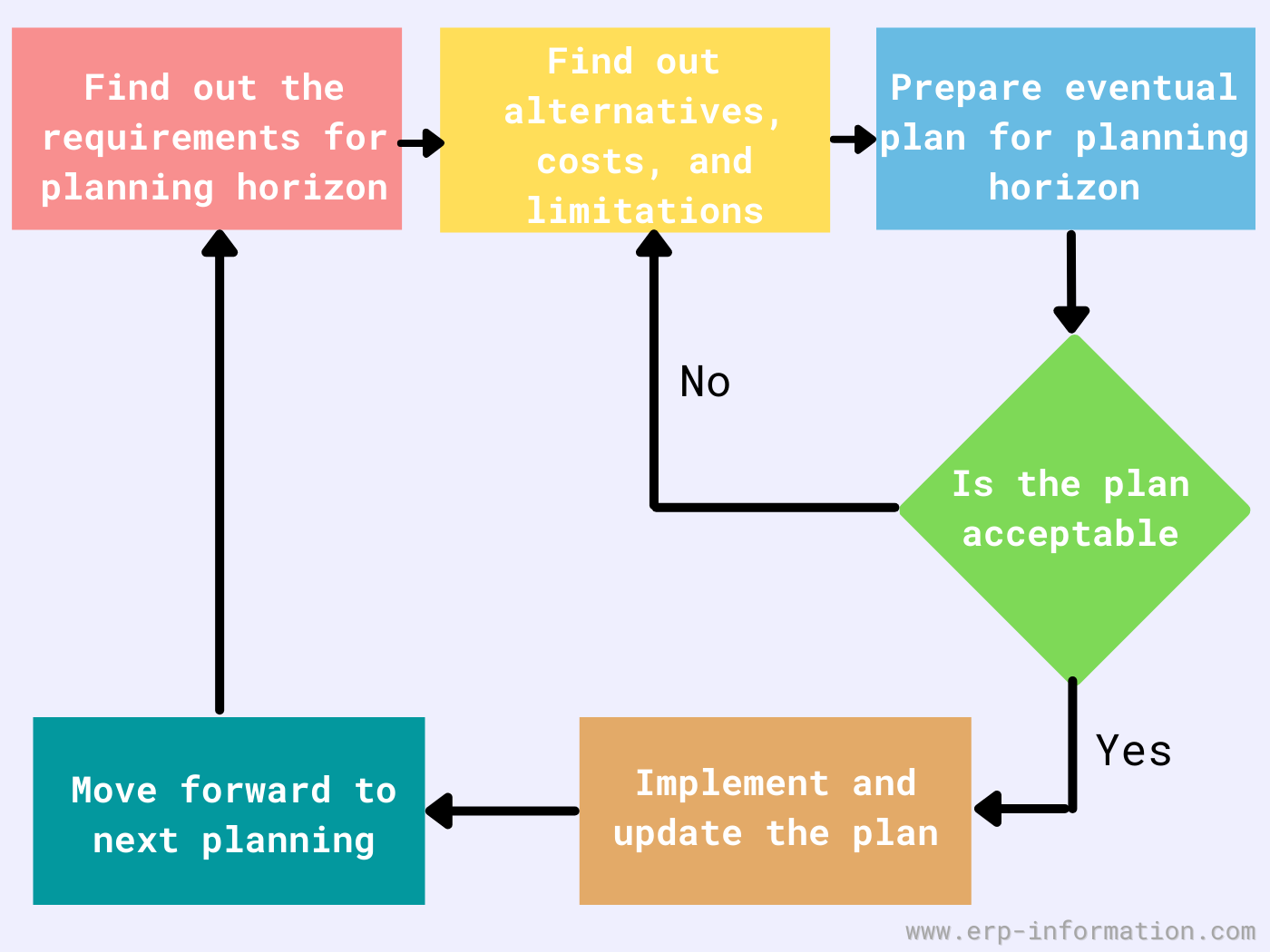



What Is Aggregate Planning 3 Strategies For Aggregate Production Planning




Strategic Supply Chain Management Aggregate Planning From Sustainability Daily News
Role of Aggregate Planning in a Supply Chain Basic Assumptions – Capacity has a cost – Lead times are greater than zero Aggregate planning – Is the process by which a company determines levels of capacity, production, subcontracting, inventory, stockouts, and pricing over a specified time horizon – goal is to maximize profit Or, if demand is effectively fixed for all theMar 04, 21 · Changes in production level cost $100 per unit due to hiring, line changeover costs, and so forth Assume 0 units of initial inventory Extra capacity may be obtained by subcontracting at an additional cost of $15 per unit over and above the company's producing them itself on regular timeApr 09, 18 · Aggregate production plans facilitate matching of supply and demand while reducing costs Process of Aggregate production planning applies the upperlevel predictions to lowerlevel, productionfloor scheduling and is most successful when applied to periods 2 to 18 months in the future



Chapter 12 Aggregate Planning Doc Inventory Mathematical Optimization
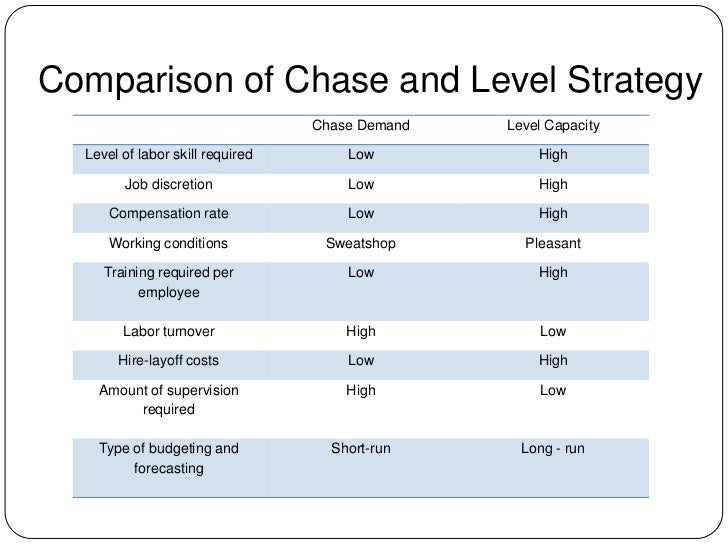



Aggregate Planning Report
A large distribution center must develop a staffing plan that minimizes the total cost using parttime workers Use chase and level strategy and compute the total cost • Each period is hours • From the beginning manager has 10 parttime workers • The distribution center can hire new parttime workers in any period, but no more thanProcessed The aggregate production approach is predicated on the existence of an aggregate unit of production, such as the \average" item, or in terms of weight, volume, production time, or dollar value Plans are then based on aggregate demand for one or more aggregate items OnceAggregate Planning a Level Work Force Plan `backorders allowed `constant numbers of workers Aggregate Planning Available capacity 50 50 10 12 14 16 0 350 150 50 75 75 0 300 300 12 14 0 350 350 Demand 1050 Excess capacity Ending inventory 123 Beginning inventory Period 1
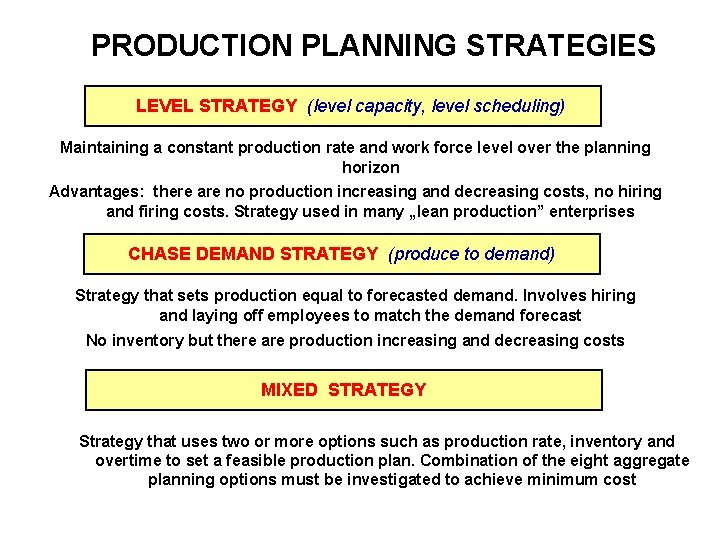



Sales And Operations Planning Aggregate Planning Production Planning




Aggregate Planning An Overview Sciencedirect Topics
Jun 15, 21 · Defining the concept of aggregate plan for operational capacity management, which strategy (Level or Chase) do you think would be best applicable for the company Operations Management List and explain in brief the various types of plant layout concepts in operations management, highlighting the objective, considerations of a good layout designJul 19, 19 · Aggregate planning is concerned with determining the quantity and the schedule of production for the immediate future Aggregate plans are intermediaterange plans that are valid for three to 18 months The main objective of aggregate plans is to lower costs and to use capacity most efficiently The operations department uses the forecasted demand for the planning periodJan 14, · The primary difference among the three strategies is the lever, that is, the parameter that is manipulated to achieve equality of supply and demand over the aggregate planning period The first chase strategy uses capacity, in the form of machine or personnel capacity, as the lever



Aggregate Planning Strategies Of Scm Inventory Demand
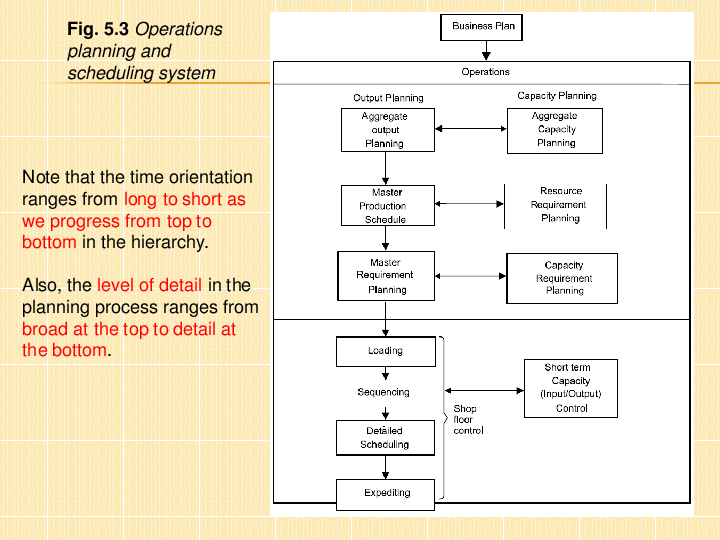



Ppt 1 Aggregate Planning Operations And Supply Management The Core Nilufer Tekkol Academia Edu
Intermediaterange capacity planning Usually covers a period of 12 months Short range Intermediate range Long range Now 2 months 1 Year Aggregate Planning Longrange plans Long term capacity Location / Layout Intermediate plans (Aggregate Planning) Manpower Utilization regular time, overtime Outsourcing Buying from a third party Inventory carrying product for latterDec 17, · the production level, inventory level, and capacity for each period the production level, staffing level, and capacity for each period Q51 – Aggregate planning solves problems involving aggregate decisions or stock keeping unit (SKU) level decisions stock keeping unit (SKU) level decisions rather than aggregate decisions1 The utilization of operational resources throughout the year 2 Efficient level of production can be maintained 3 Decreases the marginal cost The disadvantages of the level capacity strategy include 1 If there is any change in the demand of the customer there is a risk of obsolescence
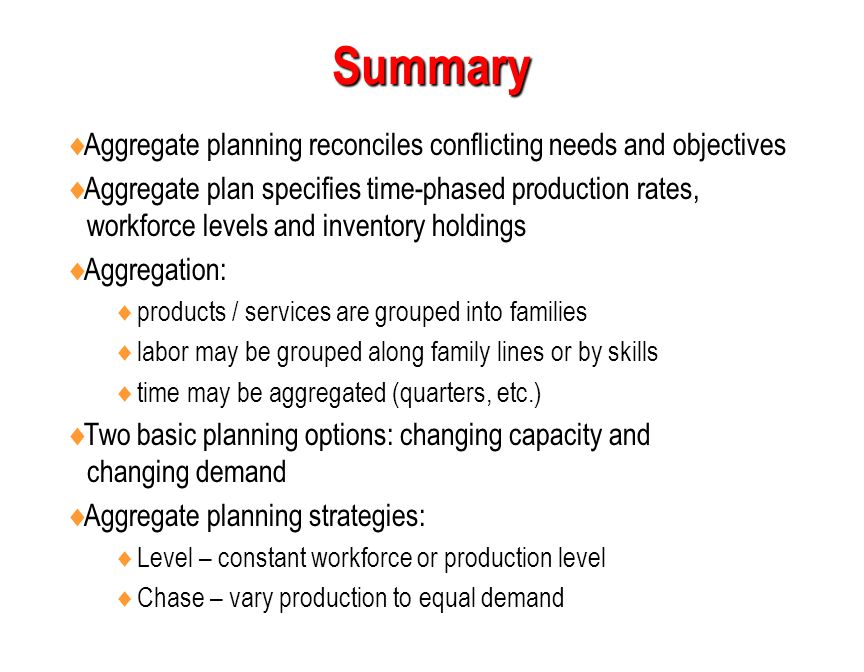



Aggregate Planning Ppt Download



1
Jun 28, 13 · The plant uses a backlog of orders to allow a levelcapacity aggregate plan This plan provides a weekly capacity of 5,000 labor hours Texprint's roughdraft of an MPS for its printers is shown on the next slide Does enough capacity exist to execute the MPS?




Logistics And Supply Chain Forum Aggregate Production Planning Part I



Http Citeseerx Ist Psu Edu Viewdoc Download Doi 10 1 1 681 8198 Rep Rep1 Type Pdf




Sales And Operations Planning Aggregate Planning Production Planning Operations Planning How To Meet Effectively And Efficiently Forecasted Requirements Ppt Video Online Download



1
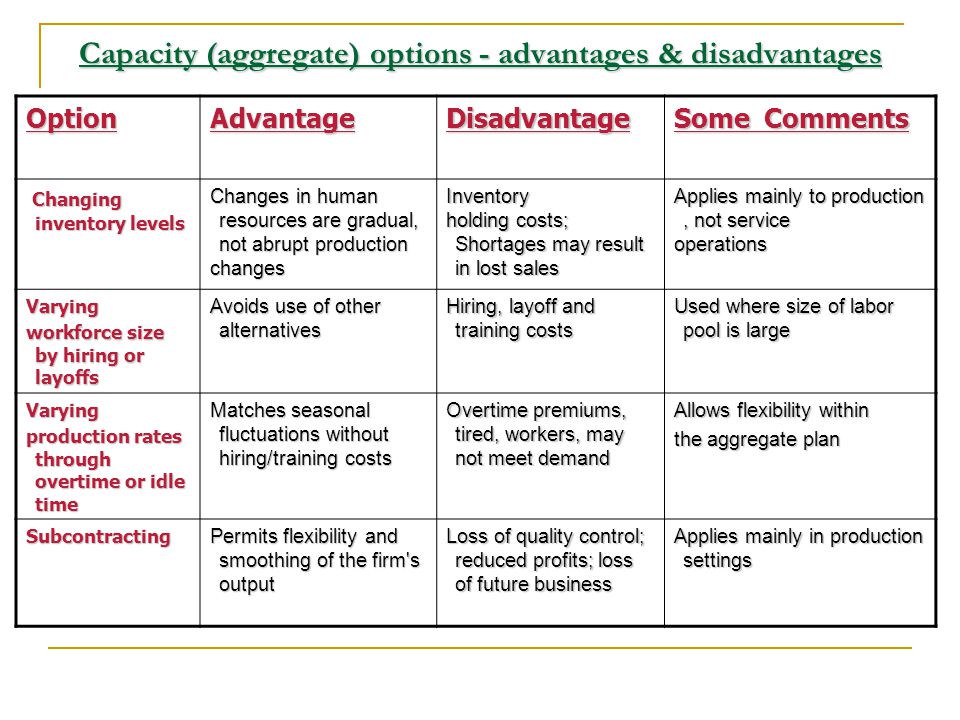



Aggregate Production Planning Ppt Video Online Download



1



Aggregate Planning Strategies Of Scm Inventory Demand



Sustainability In Supply Chain Management Aggregate Planning From Sustainability Perspective



Solved Number Of Employees At The Start Of The Tint Quarter 126 Coat Per I Plcyee Number Of Units Produced Per Employee Overtime Demand For The Rst Course Hero




Chapter 13 Aggregate Planning Ppt Video Online Download
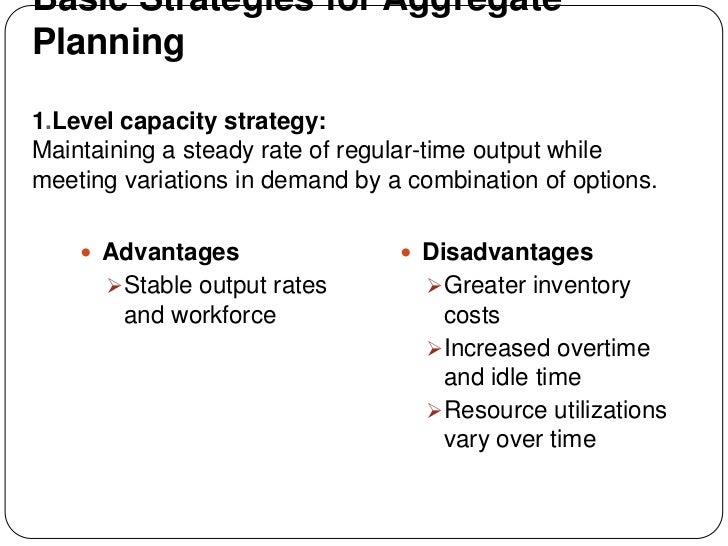



Aggregate Planning Report




Aggregate Planning Strategy Organization Levels System Examples Model Type Company System



Myclass Dau Edu cswebdav Xid 4 2



M Dc Operations Strategy
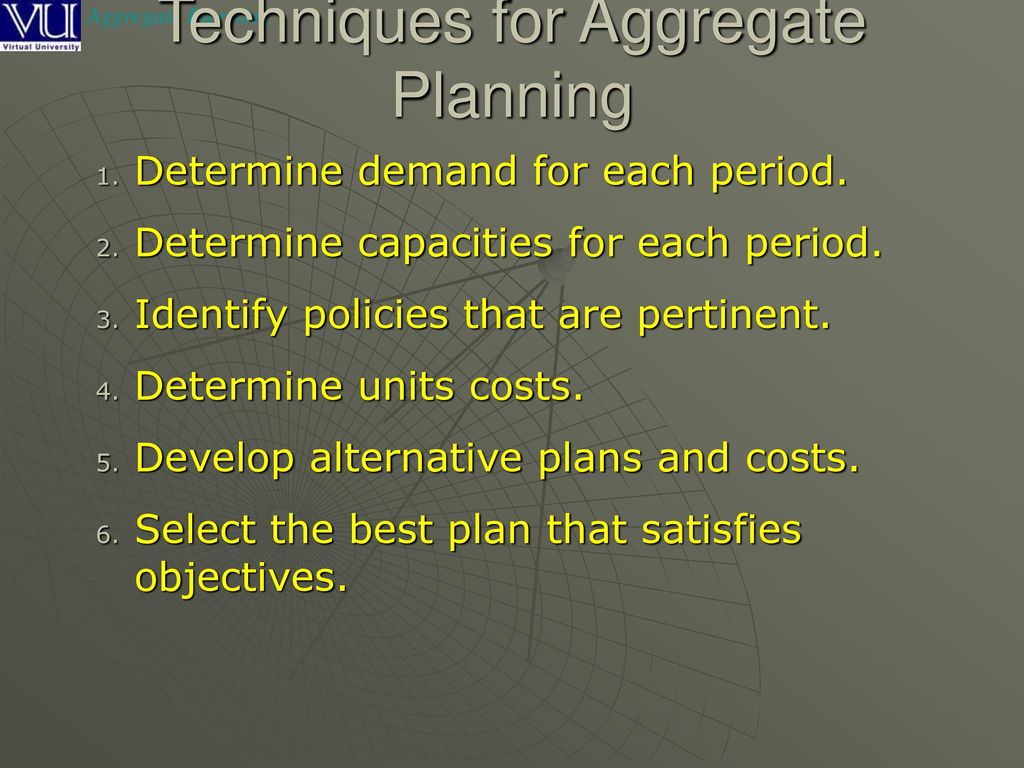



Basic Strategies Level Capacity Strategy Chase Demand Strategy Ppt Download



1
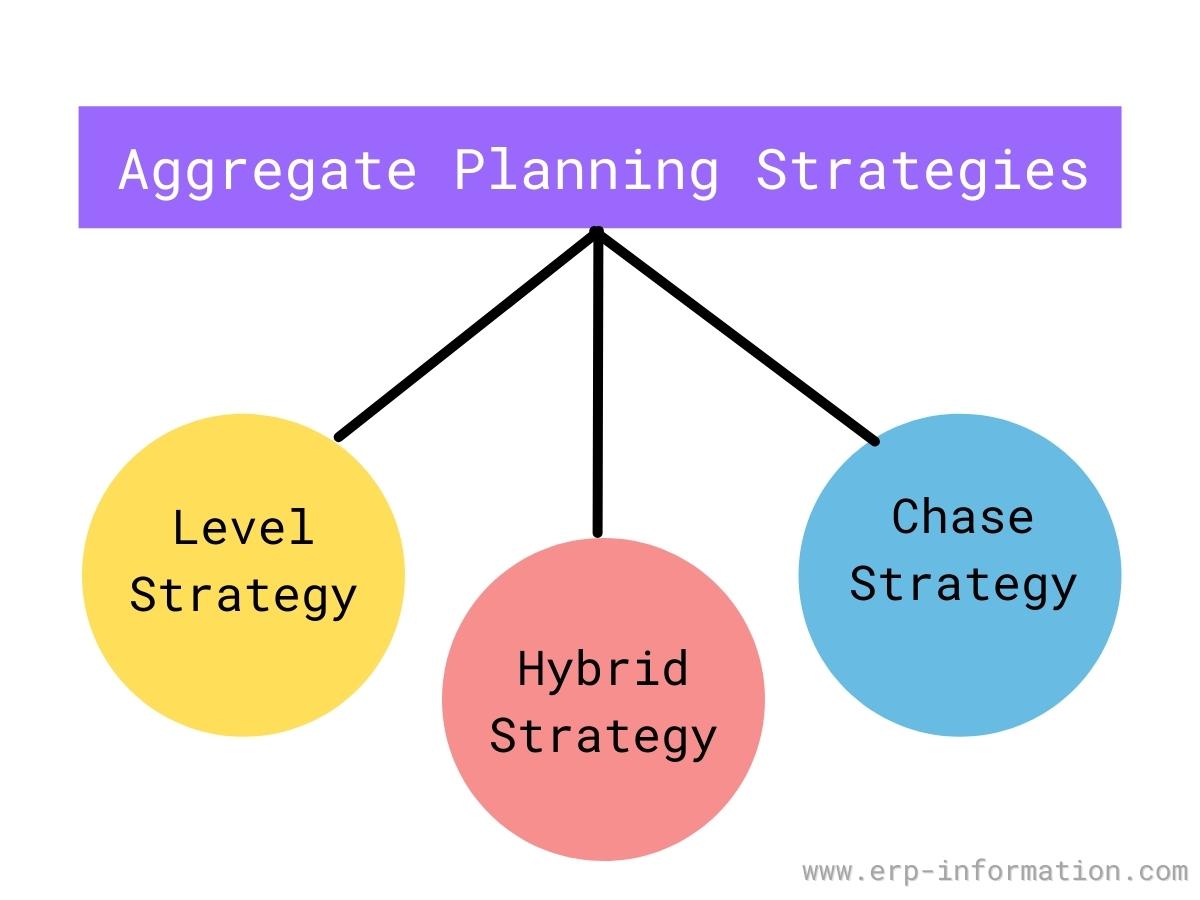



What Is Aggregate Planning 3 Strategies For Aggregate Production Planning
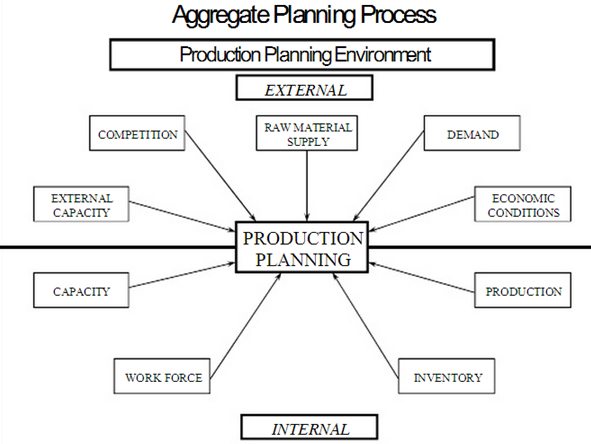



Aggregate Production Planning Aggregate Planning Process Aggregate Production Planning Strategies
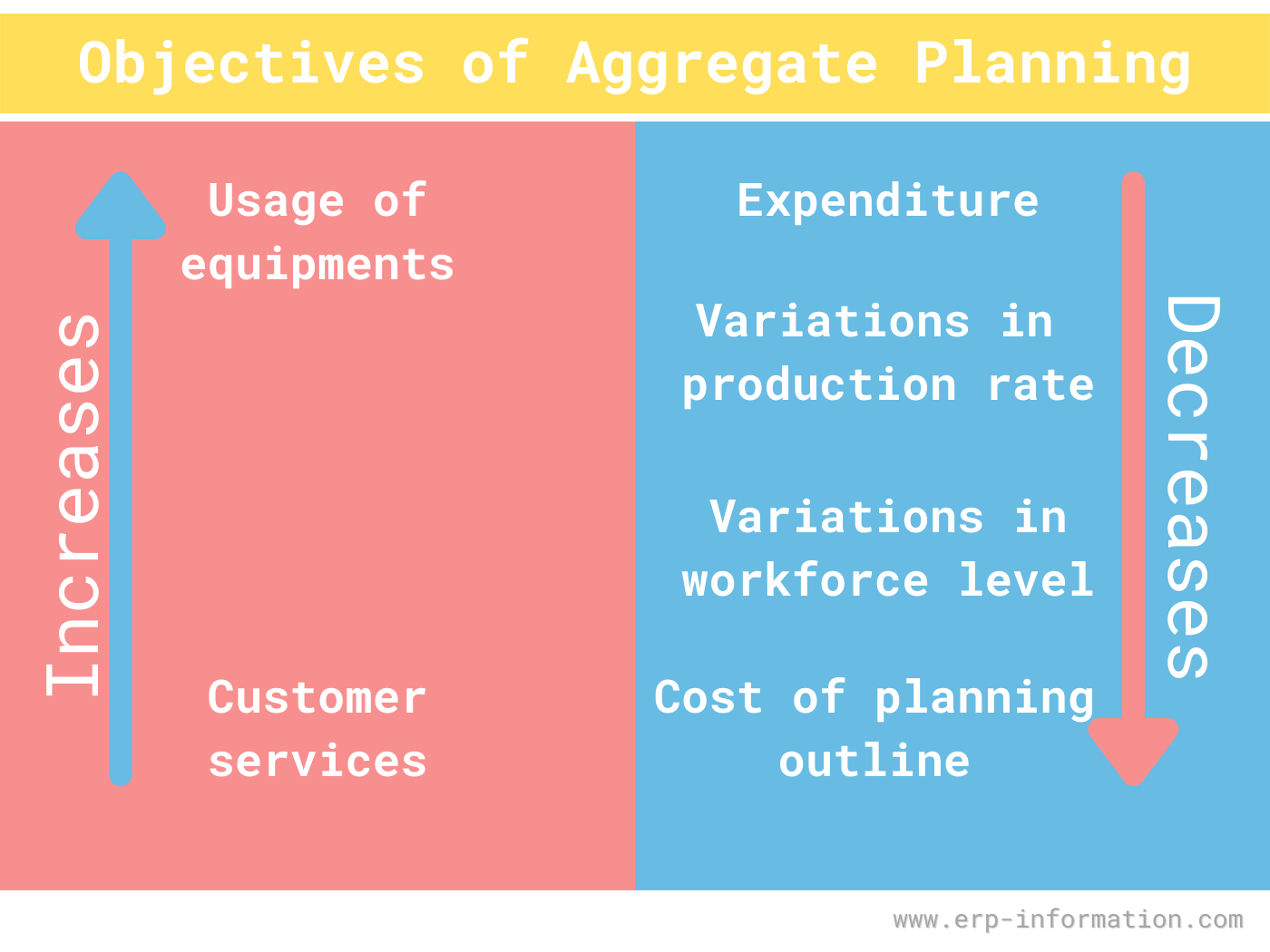



What Is Aggregate Planning 3 Strategies For Aggregate Production Planning
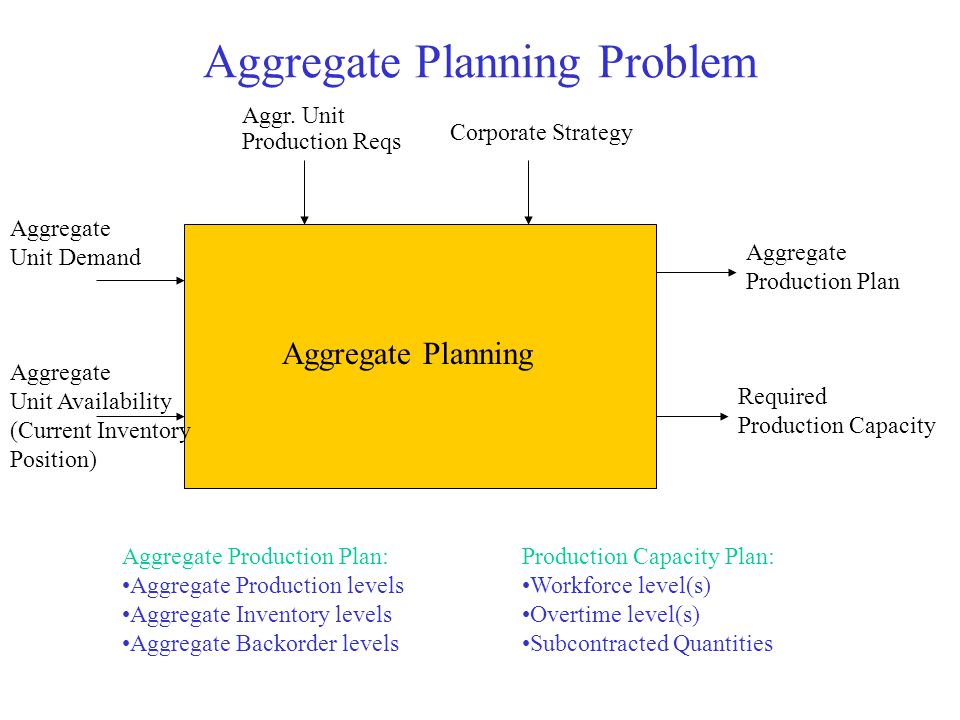



Production Planning Scheduling In Large Corporations Ppt Download
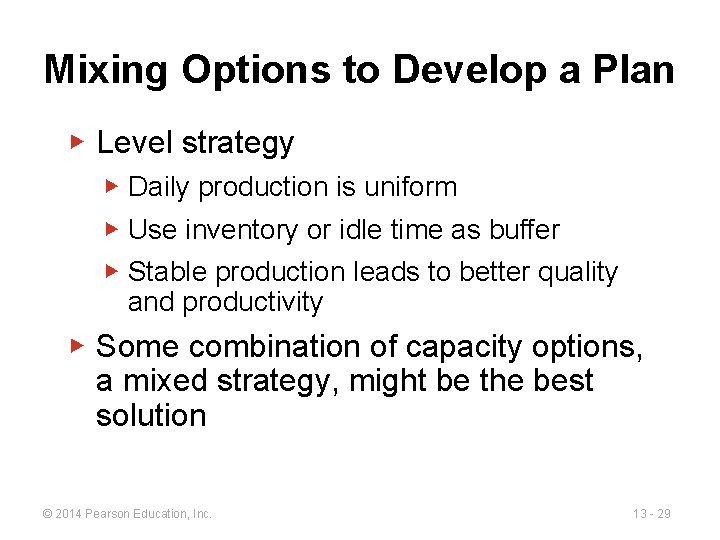



Aggregate Planning And Sop 13 Power Point Presentation




Operations Management Aggregate Planning Assignment
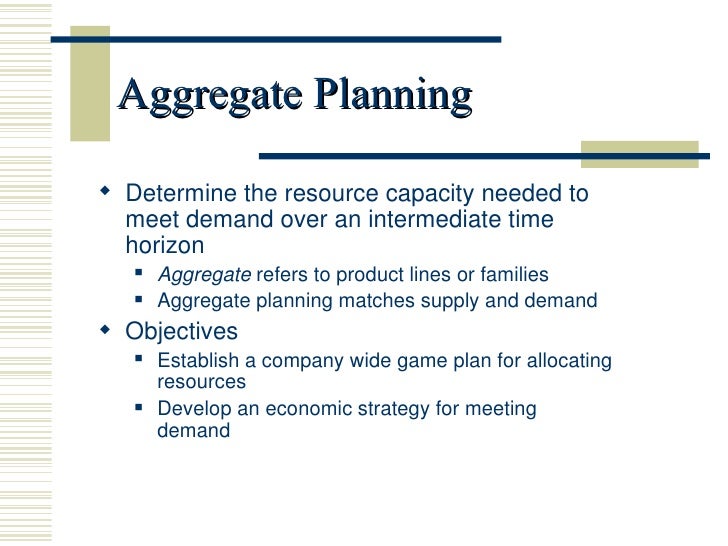



Aggregate Planning



Aggregate Planning Techniques Operations Management Homework And Assignment Help
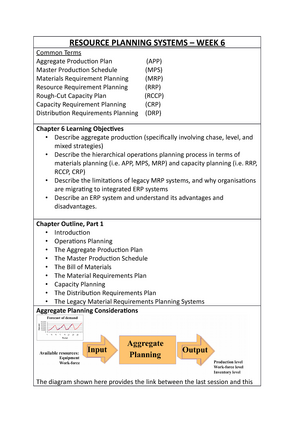



Week 6 Resource Planning System Studocu
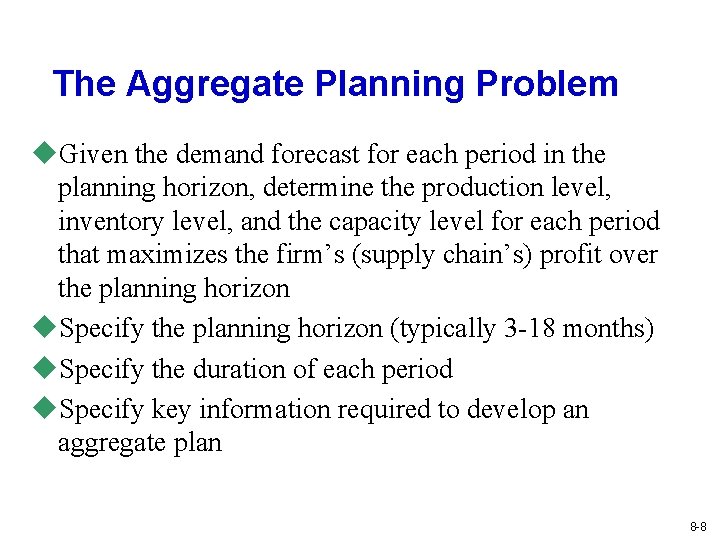



Supply Chain Management Chapter 8 Aggregate Planning In
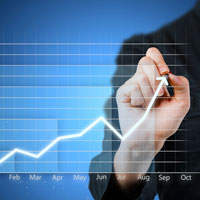



Aggregate Planning And Forecasting
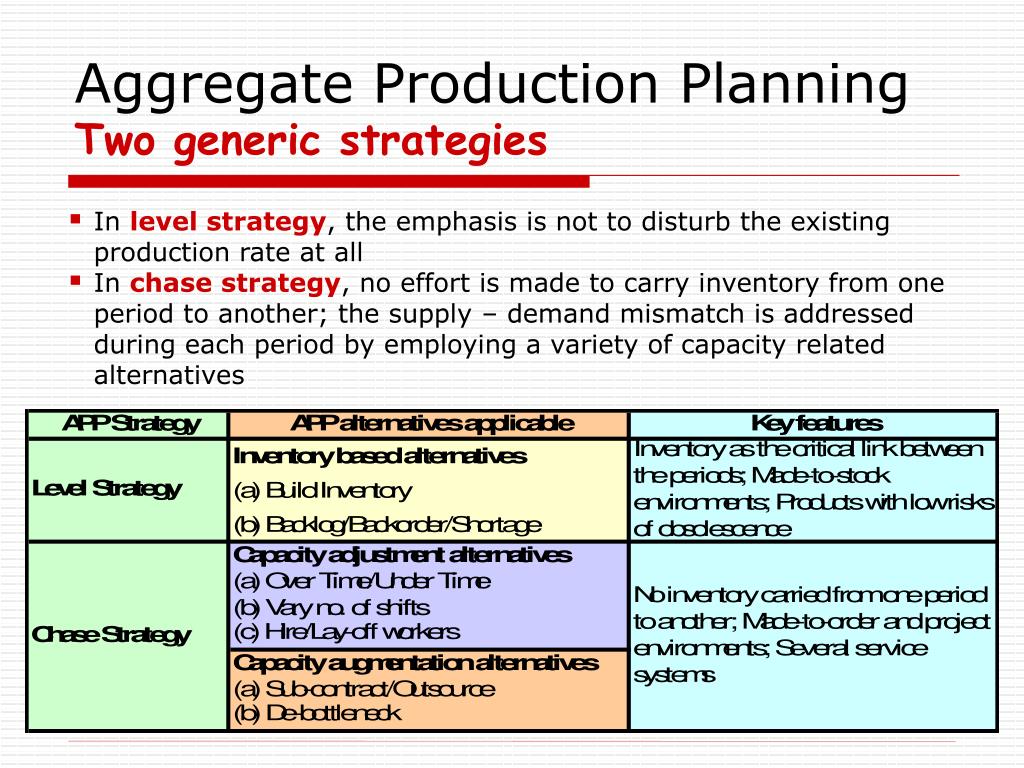



Ppt Aggregate Production Planning Powerpoint Presentation Free Download Id




Aggregate Planning Ppt Download



Master Production Schedule




Decision Variables And Cost In Aggregate Planning Download Table
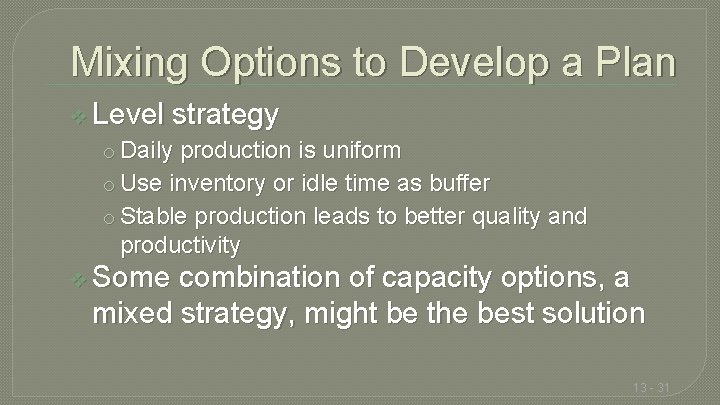



Chapter 13 Aggregate Planning And Sop 14 Pearson
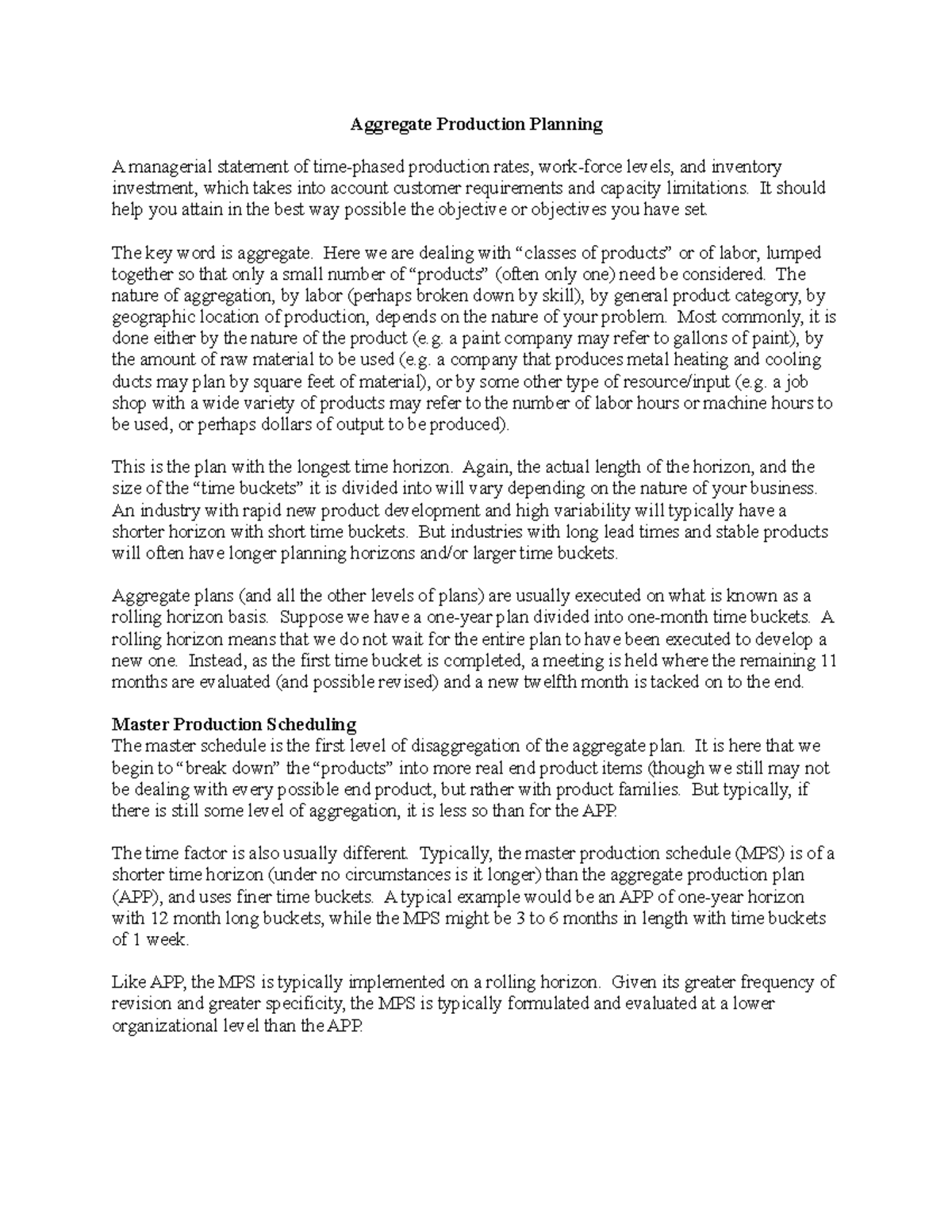



71bocywih6un0m
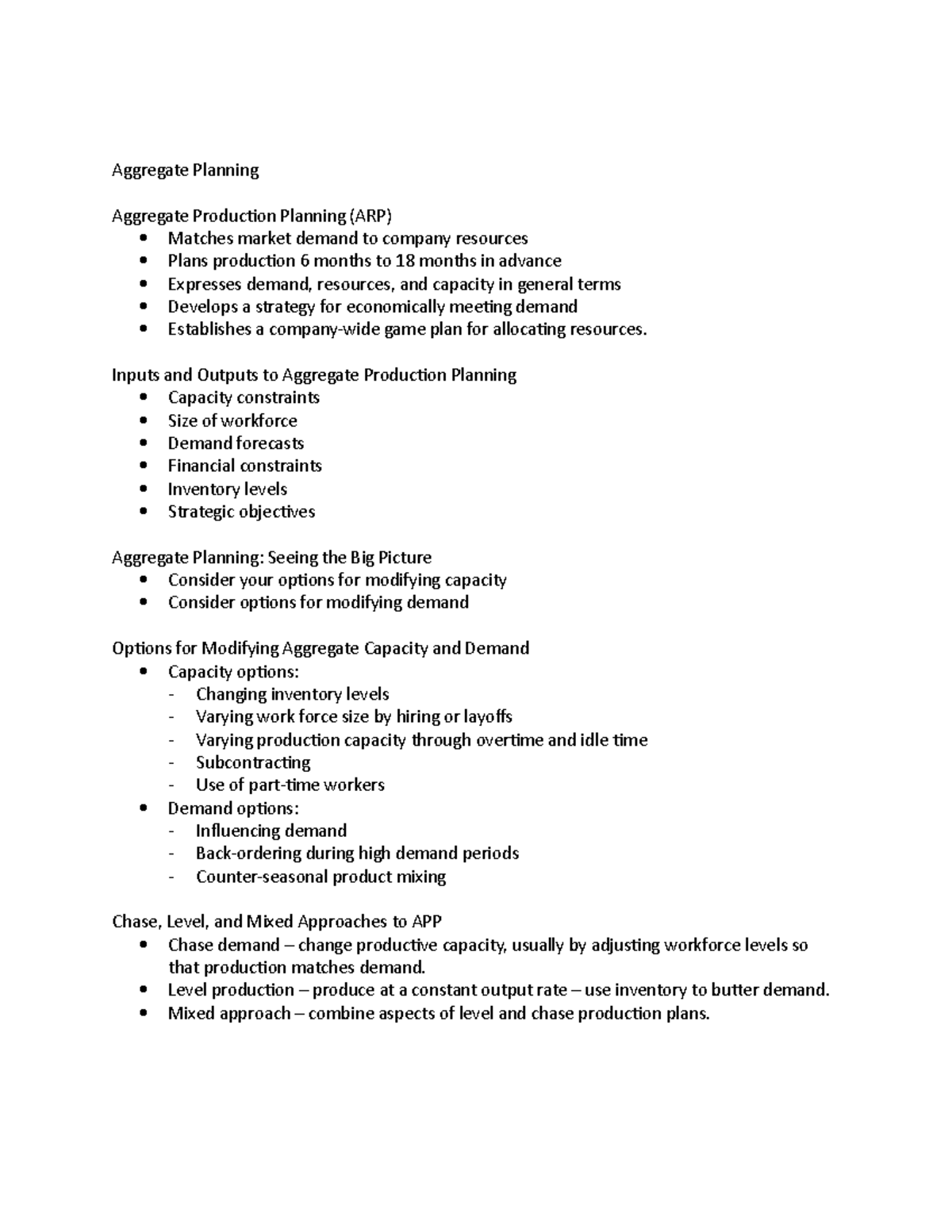



Aggregate Planning Lecture Notes 10 14 Studocu
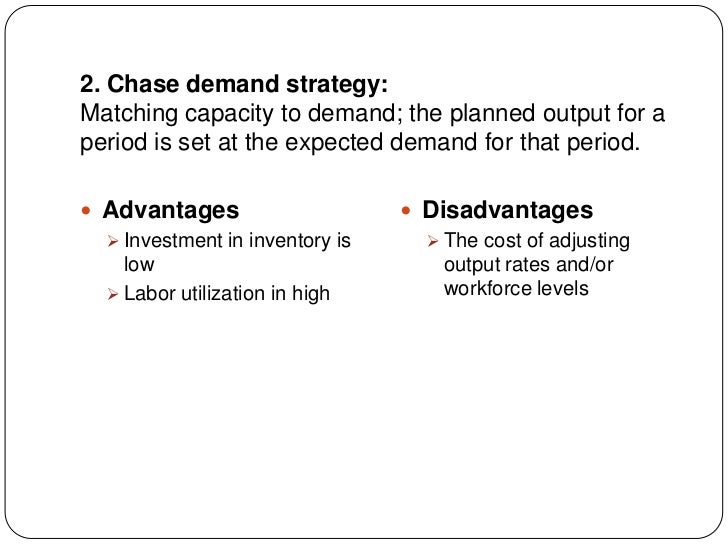



Aggregate Planning Report
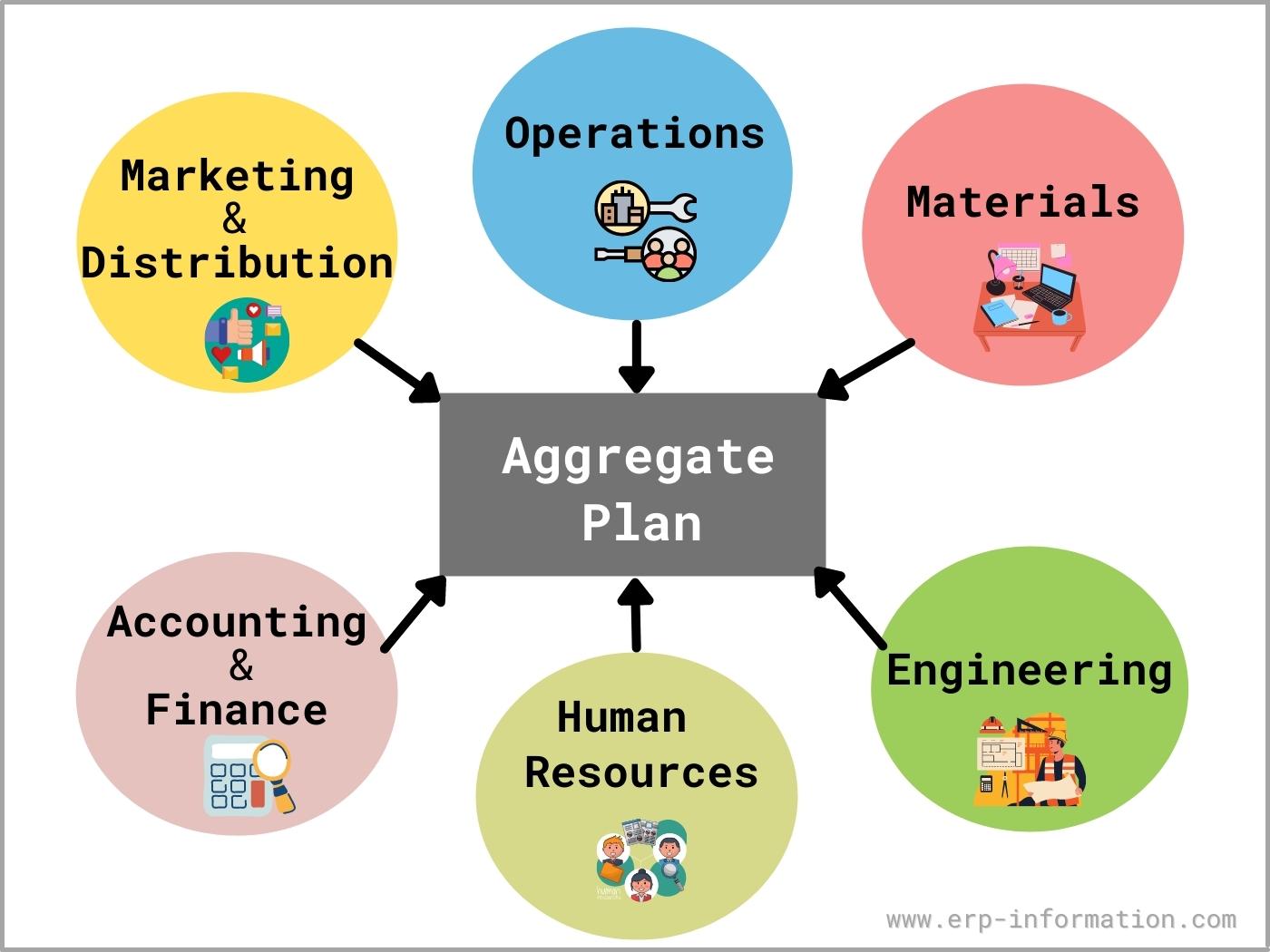



What Is Aggregate Planning 3 Strategies For Aggregate Production Planning
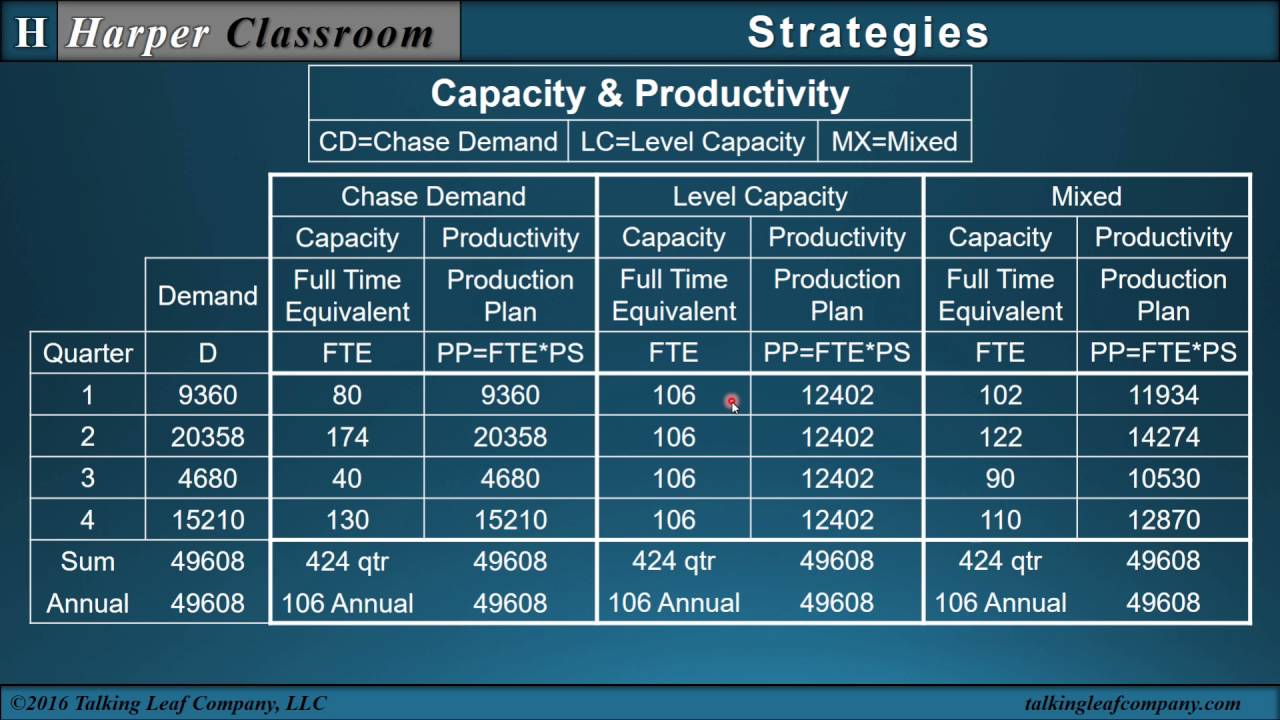



Aggregate Planning Strategies With Excel Dr Harper S Classroom Youtube



Myclass Dau Edu cswebdav Xid 4 2
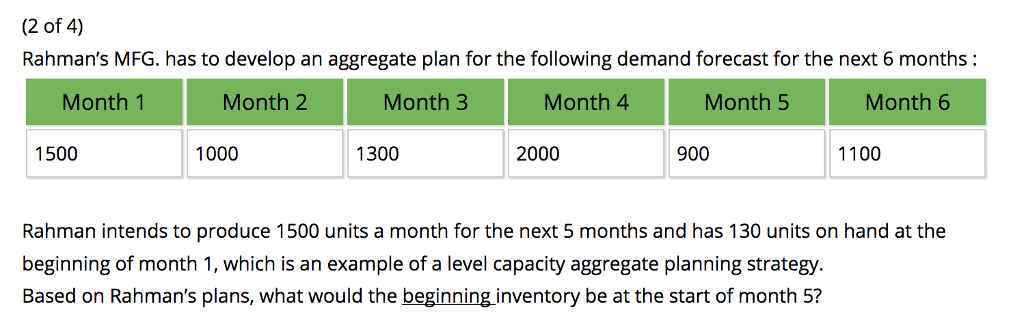



Solved 2 Of 4 Rahman S Mfg Has To Develop An Aggregate Chegg Com
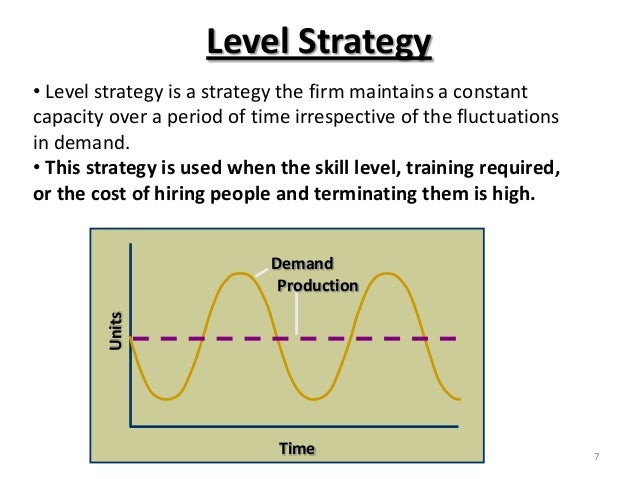



Models Of Aggregate Planning



Larry Smith The Manager Of Cases For You Wants To Use Aggregate Planning For The Company S Line Of Rugged Carryon Suitcases Below Is The Company S Course Hero
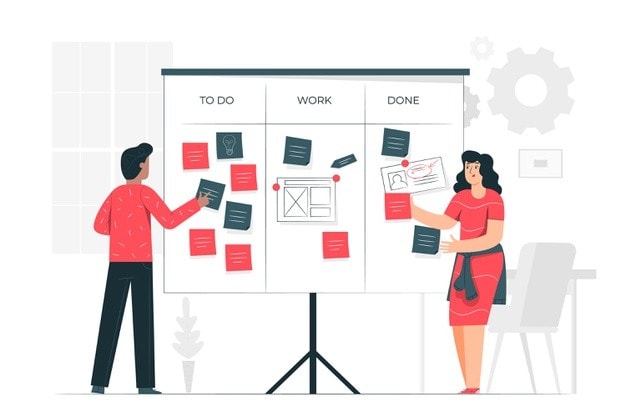



Aggregate Planning Definition Importance Strategies Management And Advantages
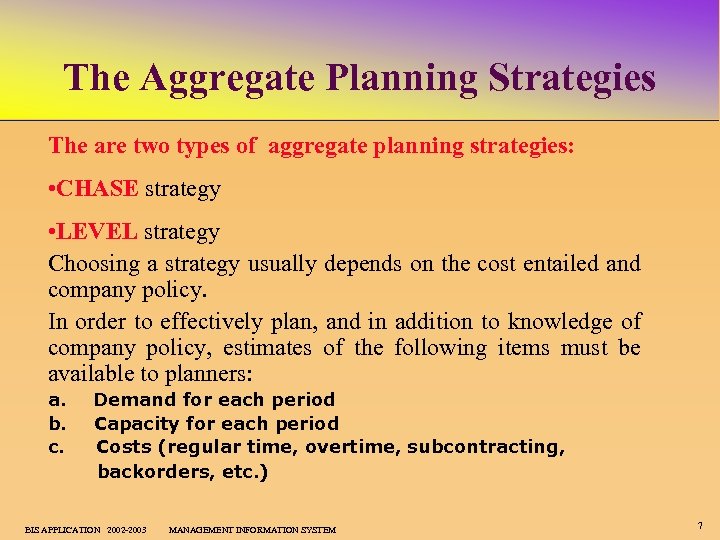



Aggregate Planning And Learning Curves Chapter Outline 1



Methods For Aggregate Planning Inventory Labour Economics




Aggregate Plan And Master Production Schedule Linkage Springerlink
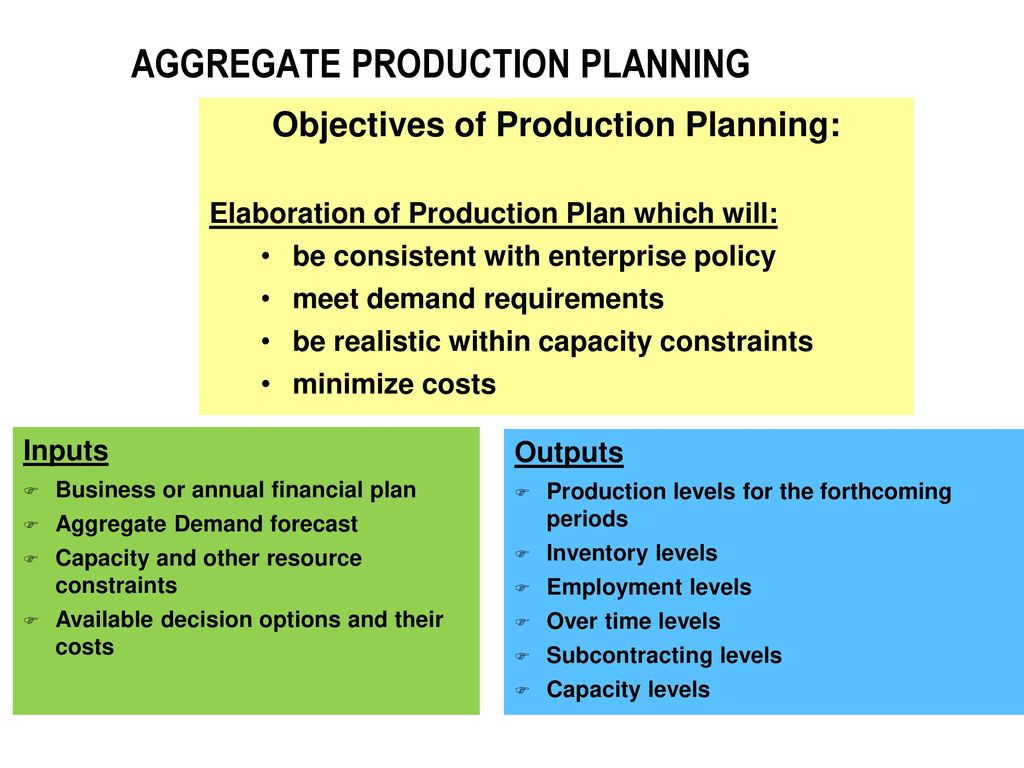



Sales And Operations Planning Aggregate Planning Production Planning Operations Planning How To Meet Effectively And Efficiently Forecasted Requirements Ppt Video Online Download
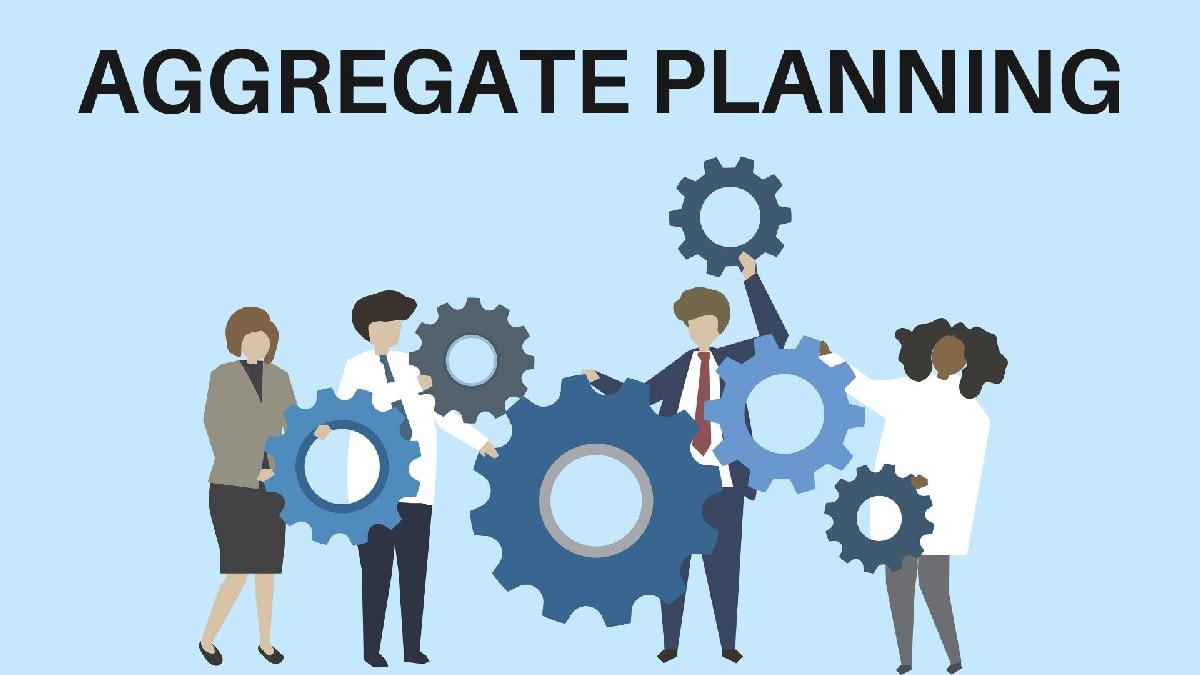



Aggregate Planning Definition Importance Strategies Management And Advantages
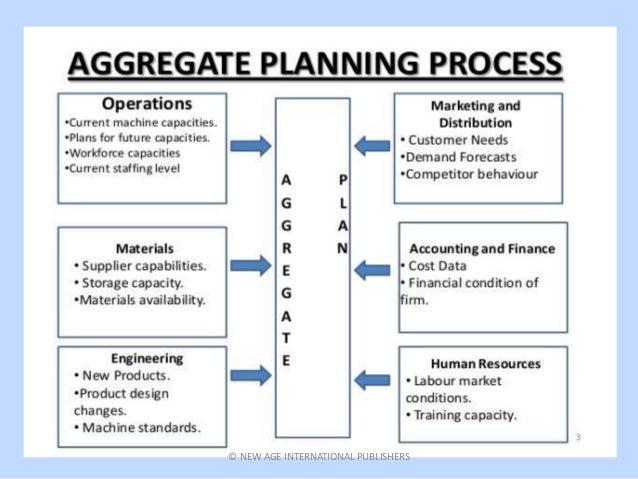



Capacity Aggregate Planning




Decision Variables And Cost In Aggregate Planning Download Table




Master Production Schedule Mps In Production And Operations Management Tutorial 30 June 21 Learn Master Production Schedule Mps In Production And Operations Management Tutorial 9613 Wisdom Jobs India




Pdf Optimal Control Approaches To The Aggregate Production Planning Problem



Operations Management Focusing On Quality And Competitiveness
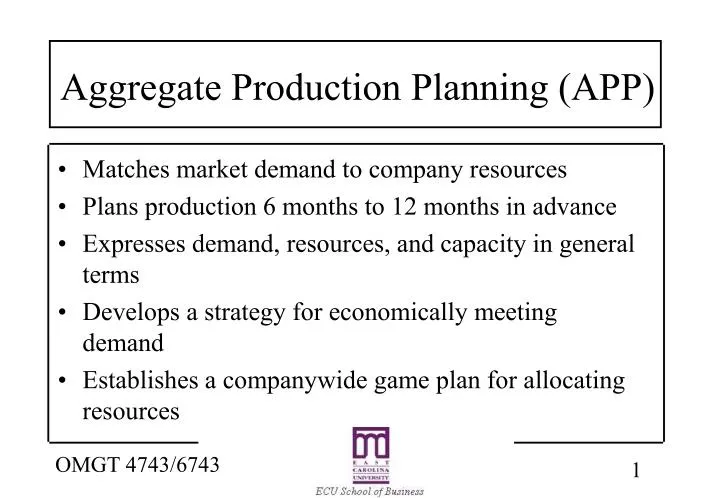



Ppt Aggregate Production Planning App Powerpoint Presentation Free Download Id
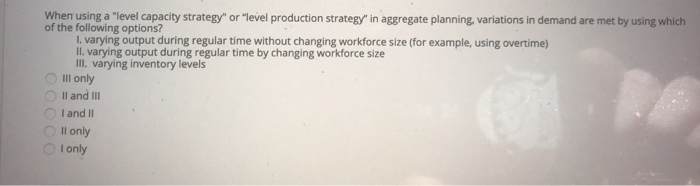



Solved When Using A Level Capacity Strategy Or Level P Chegg Com



Myclass Dau Edu cswebdav Xid 4 2
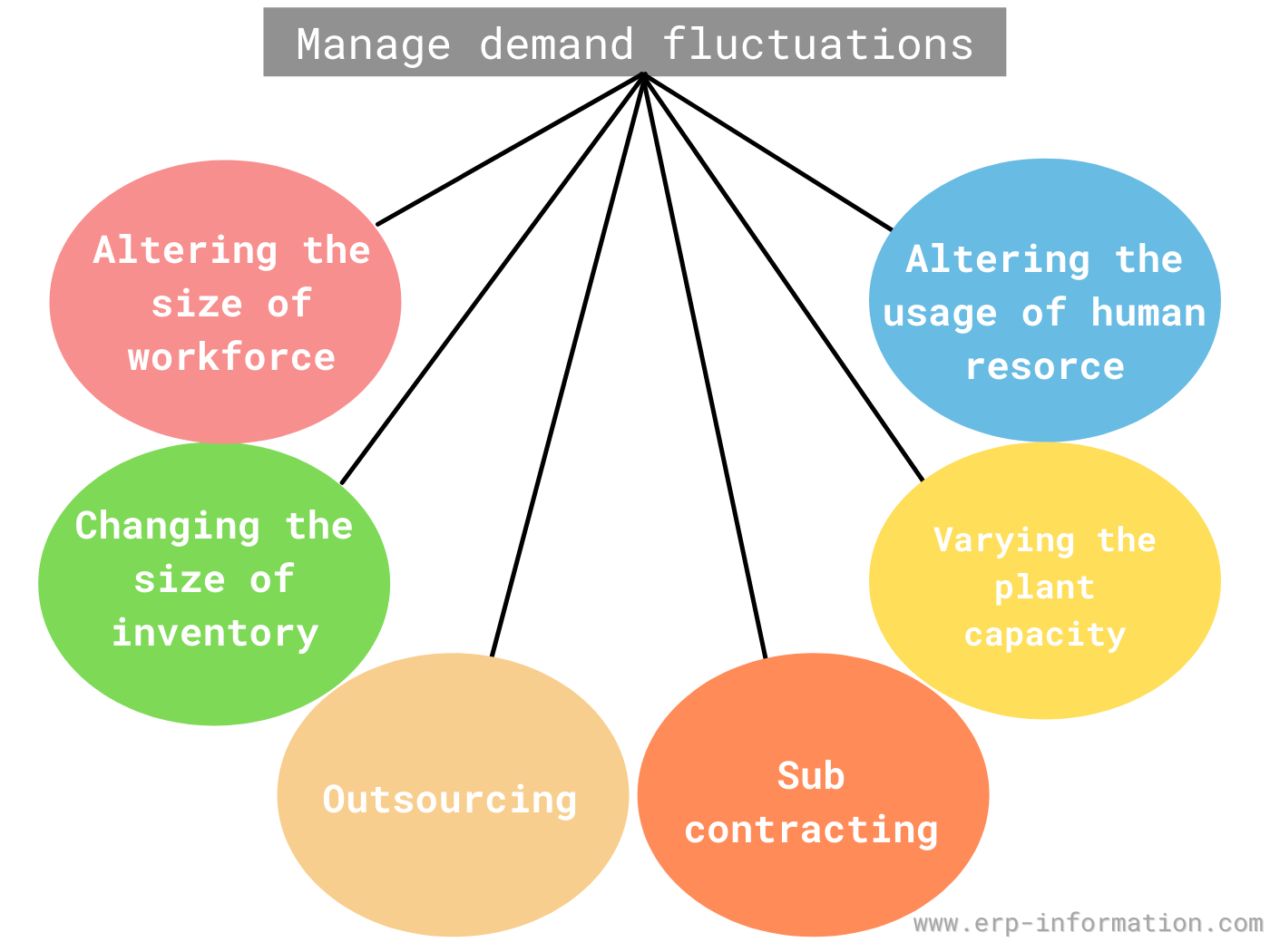



What Is Aggregate Planning 3 Strategies For Aggregate Production Planning
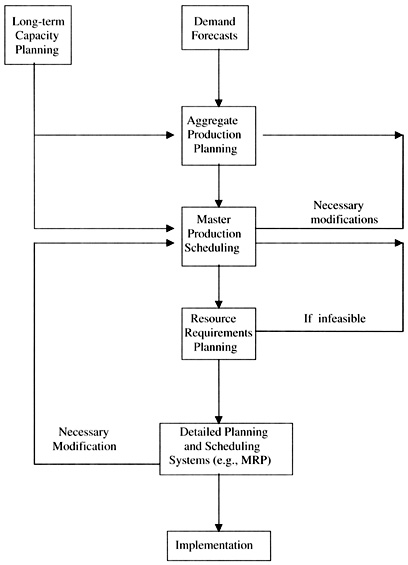



Aggregate Plan And Master Production Schedule Linkage Springerlink
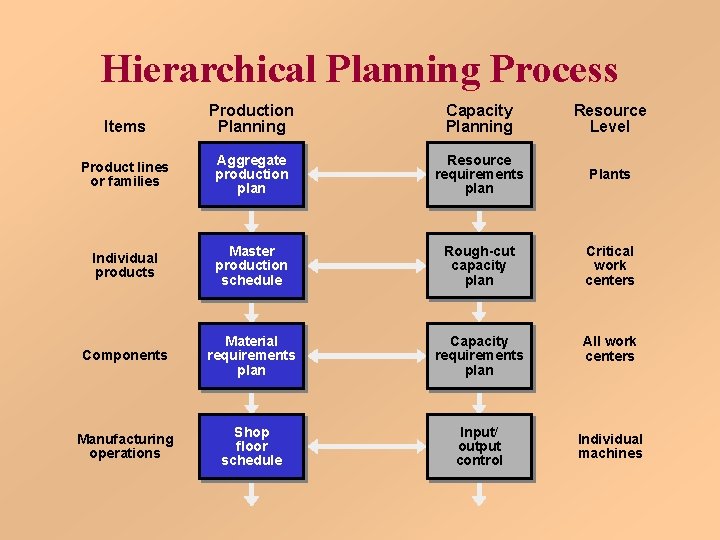



Aggregate Planning 2 Aggregate Planning Aggregate Planning Intermediaterange



Aggregate Planning Scheduling Production Processes Operations Management
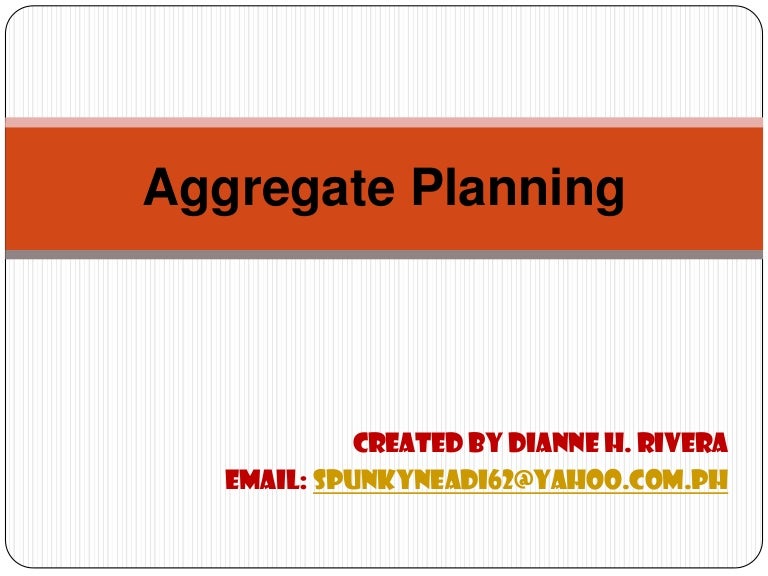



Aggregate Planning Report




Aggregate Planning An Overview Sciencedirect Topics




Aggregate Planning Strategy Organization Levels System Examples Model Type Company System




Decision Variables And Cost In Aggregate Planning Download Table



Myclass Dau Edu cswebdav Xid 4 2




Problems Into The Company Production Planning Process Download Scientific Diagram
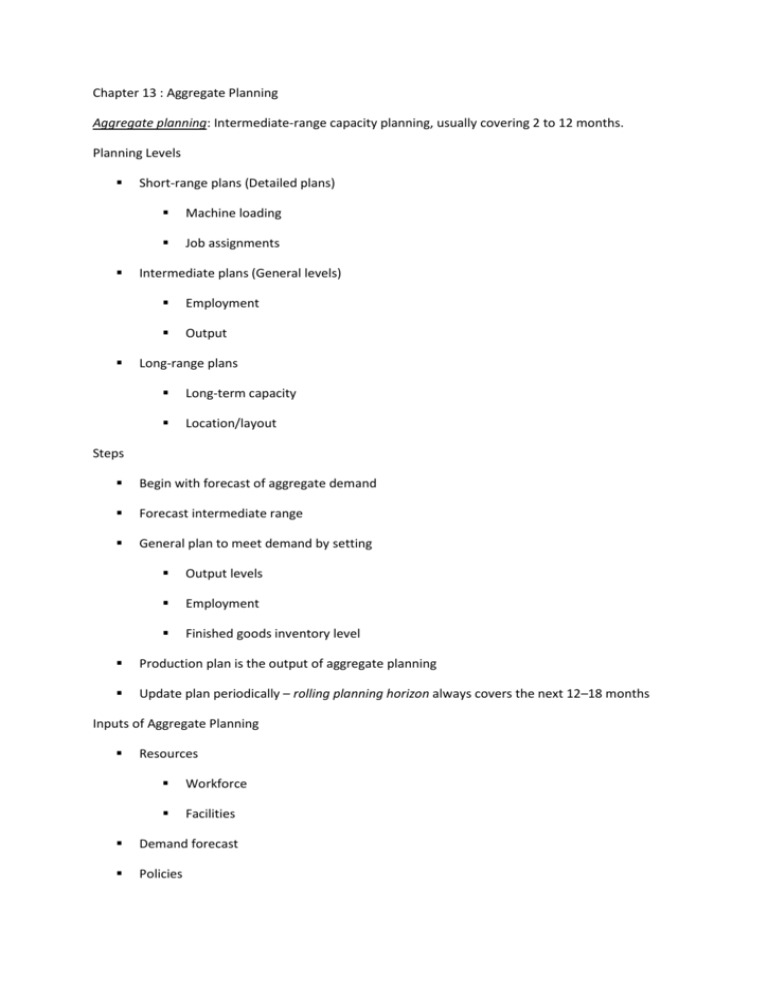



Chapter 13 Aggregate Planning




Aggregate Planning An Overview Sciencedirect Topics
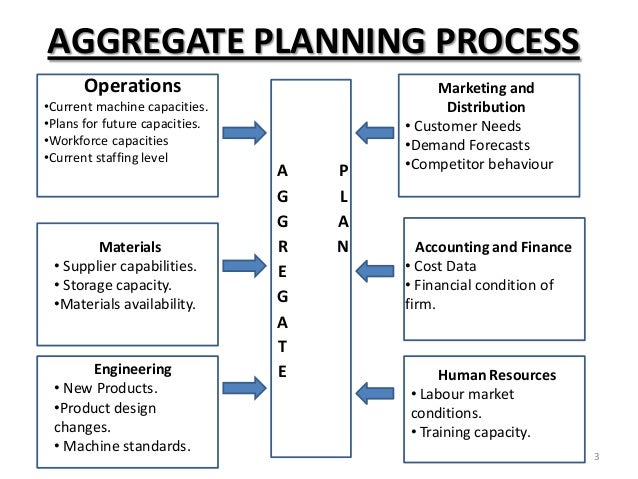



Models Of Aggregate Planning
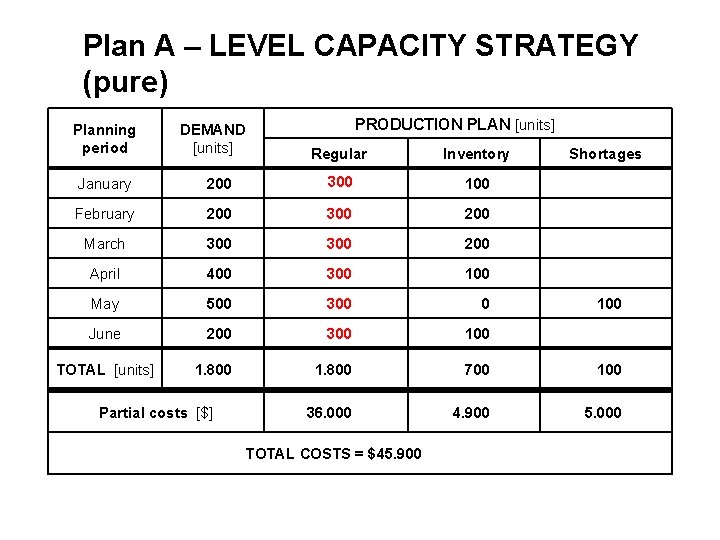



Sales And Operations Planning Aggregate Planning Production Planning



Aggregate Planning Mps Capacity Planning Strategic Management Inventory




Aggregate Planning Level Production Plan Youtube
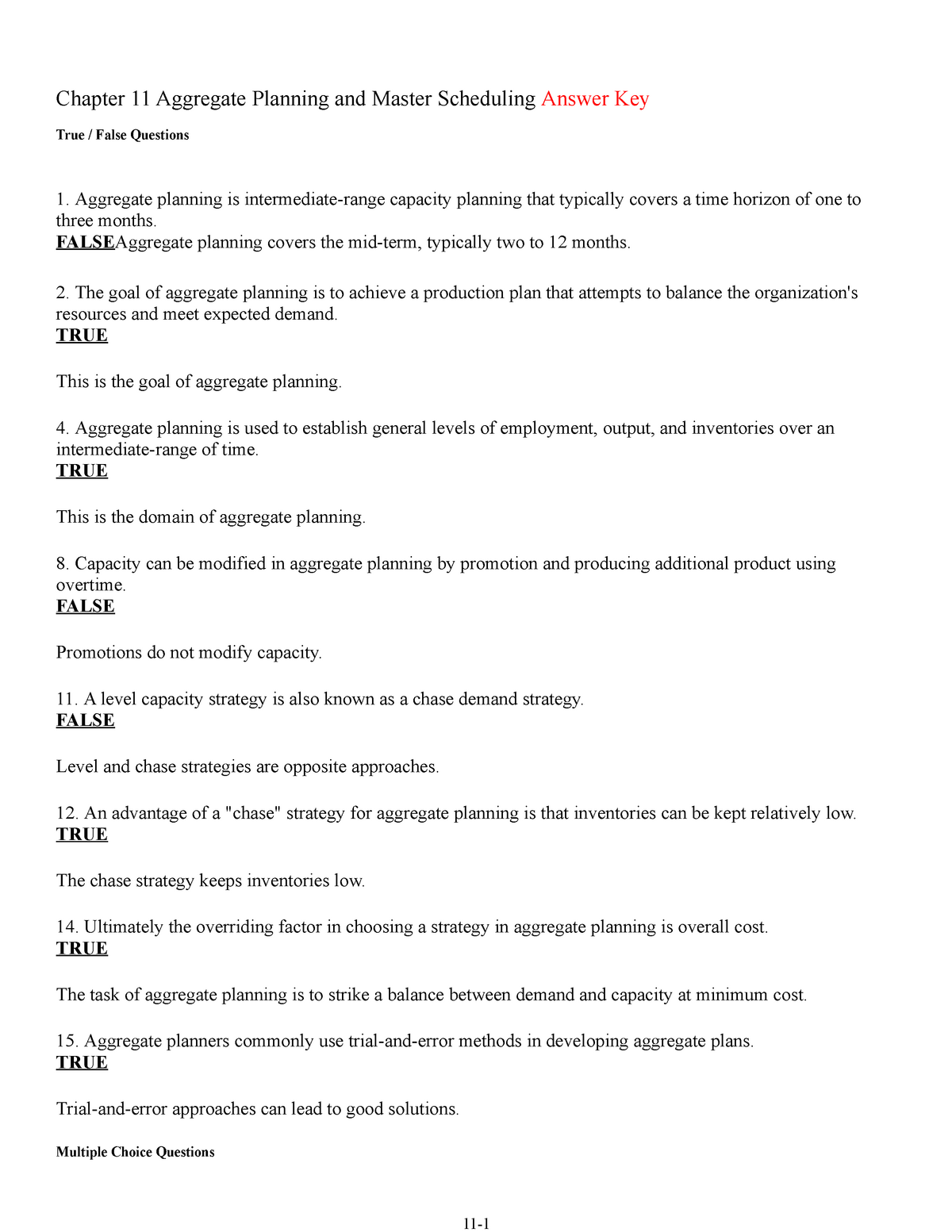



Chap011 Aggregate Chapter 11 Aggregate Planning And Master Scheduling With Answers Studocu
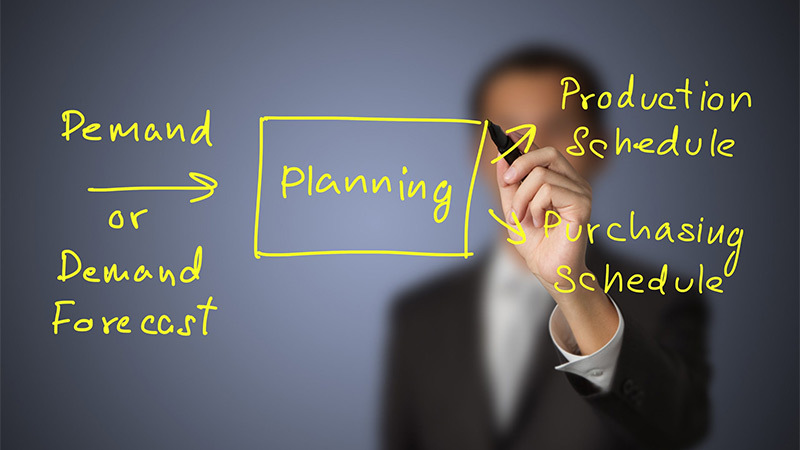



Capacity Planning An Industry Guide Plex Demandcaster
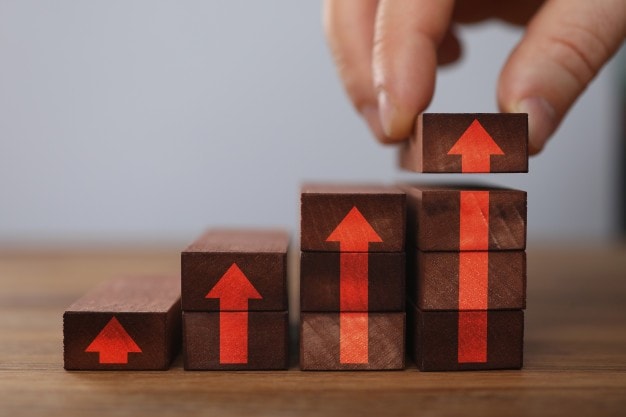



Aggregate Planning Definition Importance Strategies Management And Advantages




Which Of These Aggerate Planning Strategies Is A Capacity Option Nadex Cfpb Complaint
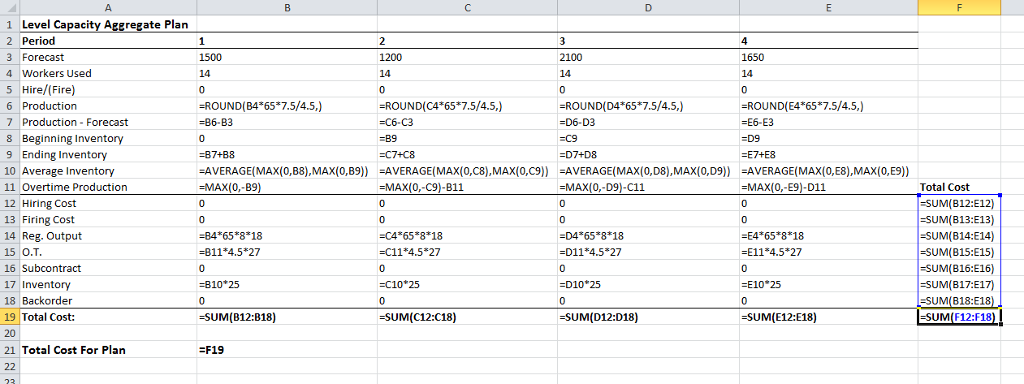



The Owner Of A Small Mill Working Plant That Builds Cabinets Is Developing His Aggregate Plan For The Next Year Answersbay



Chopra4 Tif 08 Inventory Supply Chain




Aggregate Production Planning And The Master Production Schedule




Aggregate Plans For Companies With Tangible Products Operations Management An Integrated Approach 5th Edition Book




Aggregate Planning Strategy Organization Levels System Examples Model Type Company System




Aggregate Planning Ppt Download
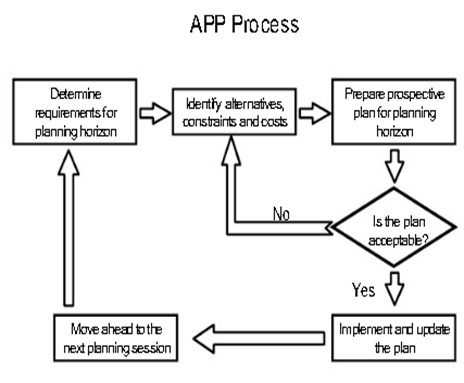



Aggregate Production Planning Aggregate Planning Process Aggregate Production Planning Strategies